Plastic Pipe
Plastic Pipe is a tubular section, or hollow cylinder, made of plastic. It is usually, but not necessarily, of circular cross-section, used mainly to convey substances which can flow—liquids and gases (fluids), slurries, powders and masses of small solids. It can also be used for structural applications; hollow pipes are far stiffer per unit weight than solid members.
Plastic pipework is used for the conveyance of drinking water, waste water, chemicals, heating fluid and cooling fluids, foodstuffs, ultra-pure liquids, slurries, gases, compressed air, irrigation, plastic pressure pipe systems, and vacuum system applications.
Types
There are three basic types of plastic pipes:
Solid Wall Pipe
Extruded pipes consisting of one layer of a homogeneous matrix of thermoplastic material which is ready for use in a pipeline.
Structured wall pipe
Structured-wall pipes and fittings are products which have an optimized design with regard to material usage to achieve the physical, mechanical and performance requirements. Structured Wall Pipes are tailor made solutions of piping systems, for a variety of applications and in most cases developed in cooperation with users.
Barrier pipe
Pipe incorporating a flexible metallic layer as the middle of three bonded layers. Barrier pipe is used, for example, to provide additional protection for the contents passing through the pipe (particularly drinking water) from aggressive chemicals or other pollution when laid in ground contaminated by previous use.
Most plastic pipe systems are made from thermoplastic materials. The production method involves melting the material, shaping and then cooling. Pipes are normally produced by extrusion.
Characteristics
Longevity of plastic piping systems
Plastic pipes have been used in service for over 50 years. The predicted lifetime of plastic piping systems exceeds 100 years. Several industry studies have demonstrated this prognosis.
Plastic pipe materials have always been classified on the basis of long-term pressure testing. The measured failure times as a function of the stresses in the pipe wall has been demonstrated in so-called Regression Curves.
An extrapolation based on measured failure times has been calculated to reach 50 years. The predicted failure stress at 50 years was taken as a basis for the classification. This value is called MRS, Minimum Required Stress, at 50 years.
Pipe system failure
Some reasons why plastic piping systems may fail are poor product bonding/gluing during installation and naturally-occurring physical damage, such as from tree root infiltration.
Flexibility
Plastic Pipes are classified by their ring stiffness. The preferred stiffness classes as described in several product standards are: SN2, SN4, SN8 and SN16, where SN is Nominal Stiffness (kN/m2). Stiffness of pipes is important if they are to withstand external loadings during installation. The higher the figure, the stiffer the pipe.
After correct installation, pipe deflection remains limited but it will continue to some extent for a while. In relation to the soil in which it is embedded, the plastic pipe behaves in a ‘flexible’ way. This means that further deflection in time depends on the settlement of the soil around the pipe.
Basically, the pipe follows the soil movement or settlement of the backfill, as technicians call it. This means that good installation of pipes will result in good soil settlement. Further deflection will remain limited.
For flexible pipes, the soil loading is distributed and supported by the surrounding soil. Stresses and strains caused by the deflection of the pipe will occur within the pipe wall. However, the induced stresses will never exceed the allowed limit values.
The thermoplastic behavior of the pipe material is such that the induced stresses are relaxing to a low level. It has to be noted that induced strains are far below the allowable levels.
This flexible behaviour means that the pipe will not fail. It will exhibit only more deflection while keeping its function without breaking.
However, rigid pipes by their very nature are not flexible and will not follow ground movements. They will bear all the ground loadings, whatever the soil settlement. This means that when a rigid pipe is subject to excessive loading, it will reach the limit for stress values more quickly and break.
It can therefore be concluded that the flexibility of plastic pipes offers an extra dimension of safety. Buried Pipes need flexibility.
PVC pipe is one of the most familiar piping plastic types, polyvinyl chloride has a number of uses beyond water transfer. It’s commonly used for main water lines, but not hot water applications since it warps at temperatures higher than 140°F.
PVC pipes are generally categorised into four: PVC-U (unplasticised PVC), C-PVC (chlorinated PVC), PVC-O (molecular oriented PVC) and modified PVC. Besides sharing many of the same properties, each type of PVC has its own advantages for different applications.
PVC-U
PVC-U stands for unplasticised PVC, which means no plasticiser (US: plasticizer) has been added to the PVC compound. Unplasticised PVC is also known as rigid PVC. PVC-U is the most common PVC type for pipes and fittings including transportation of drinking water, soil and waste, sewage and underground drainage and industrial applications.
Pipes and fittings made of PVC-U have many benefits. They are a safe choice for transportation of drinking water, light and easy to handle and affordable. Technical properties include high mechanical performance, high durability (at least 100 years for underground pipes), high chemical resistance and resistance to UV exposure. Moreover, PVC-U pipes have favorable environmental profiles and are 100% recyclable.
uPVC (unplasticized Polyvinyl Chloride)
Unplasticized polyvinyl chloride pipe for underground water mains
uPVC or PVC-U, is a thermoplastic material derived from common salt and fossil fuels. The pipe material has the longest track record of all plastic materials. The first uPVC pipes were made in the 1930s. Beginning in the 1950s, uPVC pipes were used to replace corroded metal pipes and thus bring fresh drinking water to a growing rural and later urban population. uPVC pipes are certified safe for drinking water per NSF Standard 61 and used extensively for water distribution and transmission pipelines throughout North America and around the world. uPVC is allowed for waste lines in homes and is the most often used pipe for sanitary sewers.
Further pressure and non-pressure applications in the field of sewers, soil and waste, gas (low pressure) and cable protection soon followed. The material’s contribution to public health, hygiene and well-being has therefore been significant.
Polyvinyl chloride or uPVC (unplasticized polyvinyl chloride) pipes are not well suited for hot water lines and have been restricted from inside water supply line use in the USA for homes since 2006. Code IRC P2904.5 uPVC Not listed.
uPVC has high chemical resistance across its operating temperature range, with a broad band of operating pressures. Max operating temperature is reported at 140 °F (60 °C), and max working pressure: 450 psi (3,100 kPa). Due to its long-term strength characteristics, high stiffness and cost effectiveness, uPVC systems account for a large proportion of plastic piping installations and some estimations put it that greater than 2,000,000 miles (3,200,000 km) of uPVC pipe are currently in service across applications.
uPVC Variants
Based on the standard polyvinyl chloride material, three other variants are in use.
One variant called OPVC, or PVCO, represents an important landmark in the history of plastic pipe technology. This molecular-oriented bi-axial high performance version combines higher strength with extra impact resistance.
A ductile variant is the MPVC, polyvinyl chloride modified with acrylics or chlorinated PE. This more ductile material with high fracture resistance is used in higher-demand applications where resistance against cracking and stress corrosion is important. In several studies the long track record of uPVC pipes has been investigated. Recent investigations at the German KRV and the Dutch TNO have confirmed that uPVC water pressure pipes, when installed correctly have a useful life span of over 100 years.
C-PVC
C-PVC stands for chlorinated PVC. Pipes and fittings made of C-PVC share many of PVC-U’s advantages. Both are safe for use with drinking water, have high resistance to corrosion, high durability and excellent impact resistance. However, with its higher chlorine content than regular PVC-U, pipes and fittings made of C-PVC can withstand a wider range of temperatures. This has made C-PVC a popular choice for water piping systems in residential as well as commercial construction. C-PVC is also significantly more ductile than PVC-U. Pipes and fittings made of C-PVC are 100% recyclable.
Chlorinated Polyvinyl Chloride (C-PVC) is resistant to many acids, bases, salts, paraffinic hydrocarbons, halogens and alcohols. It is not resistant to solvents, aromatics and some chlorinated hydrocarbons. It can carry higher temperature liquids than uPVC with a max operating temperature reaching 200 °F (93.3 °C). Due to its greater temperature threshold and chemical resistance, CPVC is one of the main recommended material choices in residential, commercial, and industrial water and liquid transport.
PVC-O
Molecularly oriented PVC (PVC-O) is the result of a production process that turns the amorphous structure of unplasticised PVC (PVC-U) into a layered structure.
PVC-O enhances the many benefits of PVC-U such as resistance to corrosion, preservation of water quality, cost-efficiency and recyclability and an unsurpassed balance between strength, stiffness and flexibility. Pipes made of PVC-O are especially advantageous when it comes to hydraulic capacity, ductility, crack propagation and impact and fatigue resistance. This means that PVC-O is an excellent choice for pressure pipes for drinking water. PVC-O is also well suited for buried non-potable applications such as irrigation and sewer pumping mains. PVC-O pipes and fittings are 100% recyclable.
Modified PVC (PVC-M, PVC-HI, PVC-A)
This family are thermoplastic alloys formed by the addition of compatible modifying agents to PVC. The modifying agents improve toughness, impact properties and resistance to crack growth that improves the fracture toughness and ductility of the material. This enhanced toughness enables modified PVC pipes to be manufactured with a thinner wall, with subsequent material savings and improved hydraulic properties. The alloying of PVC with modifying polymers achieves improvement in resistance to cracking. The result is the minimisation of the effect of stress concentrators such as scratches.
PVC-HI
PVC-HI stands for High Impact PVC. The PVC-HI grade is obtained by adding an impact modifier to PVC-U that increases the resistance of the pipes to external blows.
The minimum requirements for a PVC-HI grade is precisely defined in section 5 of the international standard ISO 6993-1 “Buried, high-impact poly(vinyl chloride) (PVC-HI) piping systems for the supply of gaseous fuels — Part 1: Pipes for a maximum operating pressure of 1 bar (100 kPa)”:
- Composition: PVC-HI shall be one of the following compositions:
- a mixture based on PVC
- a blend based on PVC
- a copolymer based on PVC
- a combination of these types
The proportion of the impact modifier in the composition shall be at least 7 % w
- Long term strength: The MRS value of PVC-HI shall be at least 18 MPa. Conformity to this requirement shall be proven using a long-term evaluation in accordance with ISO 9080. Testing shall be carried out at 20 °C, 40 °C and 60 °C, for periods up to 9 000 h. At 60 °C no knee shall occur before 5,000 h
- Vicat softening temperature: The Vicat softening temperature of PVC-HI shall be at least 76 °C
- K-value: The PVC-U used to make PVC-HI shall be at least 65
- Impact resistance after UV weathering: UV weathered pipe specimen of PVC-HI should not break when a striker of a defined mass is launched from a defined height
- Resistance to gas constituents: no crazes of a depth greater than 30 µm should be observed in pipe specimen of PVC-HI exposed to tetrahydrothiophene and n-hexadecane
PVC-HI transport natural gas – and is fit for hydrogen
PVC-HI is how the material should be designated when a pipe comply with ISO 6993-1 (see section 12 of the standard). This grade is the only accepted since the late 70s for pipes supplying natural gas. 60,000 km of PVC-HI pipes are installed in the Netherlands only.
PE (polyethylene)
Polyethylene has been successfully used for the safe conveyance of potable and waste water, hazardous waste, and compressed gases for many years. Two variants are HDPE Pipe (high-density polyethylene)and the more heat resistant PEX (cross-linked polyethylene, also XLPE).
PE has been used for pipes since the early 1950s. PE pipes are made by extrusion in a variety of sizes dimensions. PE is lightweight, flexible and easy to weld. Its smooth interior finish ensures good flow characteristics. Continuous development of the material has enhanced its performance, leading to rapidly increasing usage by major water and gas utility companies throughout the world.
The pipes are also used in lining and trench-less technologies, the so-called no-dig applications where the pipes are installed without digging trenches without any disruption above ground. Here the pipes may be used to line old pipe systems to reduce leakage and improve water quality. These solutions are therefore helping engineers to rehabilitate antiquated pipe systems. Excavation is minimal and the process is carried out quickly below ground.
Also for PE pipe material, several studies demonstrated the long track record with expected lifetime of more than 50 years.
Cross-linked polyethylene is commonly referred to as XLPE or PEX. It is a thermoplastic material that can be made in three different ways depending how the cross-linking of the polymer chains is being made. PEX was developed in the 1950s. It has been used for pipes in Europe since the early 1970s and has been gaining rapid popularity over the last few decades. Often supplied in coils, it is flexible and can therefore be led around structures without fittings. Its strength at temperatures ranging from below freezing up to almost boiling makes it an ideal pipe material for hot and cold water installations, radiator and under floor heating, de-icing and ceiling cooling applications.
Cross-linked polyethylene is used in home plumbing systems for hot and cold water pipes, as well as freshwater kitchen and bathroom systems. PEX pipes are generally color coded so plumbers can easily identify hot and cold lines.
PE-RT
Polyethylene of Raised Temperature (RT) or PE-RT expands the traditional properties of polyethylene. Enhanced strength at high temperatures are thus made possible through special molecular design and manufacturing process control.
Its resistance to low or high temperatures makes PE-RT ideal for a broad range of hot and cold water pipe applications.
HDPE (High-Density Polyethylene)
High-Density Polyethylene (HDPE) – HDPE pipe is strong, flexible and light weight. It has a zero leak rate when fused together.
High-density polyethylene is so tough and durable that it can be used for virtually all plumbing needs. It can also reduce water pressure since it has a low coefficient of friction, allowing water to flow easily inside.
ABS (Acrylonitrile Butadiene Styrene)
Acrylonitrile Butadiene Styrene (ABS) is used for the conveyance of potable water, slurries and chemicals. Most commonly used for DWV (drain-waste-vent) applications. It has a wide temperature range, from -40 °C to +60 °C.
ABS is a thermoplastic material and was originally developed in the early 1950s for use in oil fields and the chemical industry. The variability of the material and its relative cost effectiveness has made it a popular engineering plastic. It can be tailored to a range of applications by modifying the ratio of the individual chemical components.
They are used mainly in industrial applications where high impact strength and rigidity are essential.
This material is also used in non-pressure piping systems for soil and waste.
Short for acrylonitrile butadiene styrene, this sturdy plastic was one of the first plastics used for residential plumbing. ABS pipes are always black and tend to be softer than PVC. They are mainly used for vent and drain lines, along with other outdoor underground uses where cold temperatures are common.
PP (polypropylene)
Polypropylene is suitable for use with foodstuffs, potable and ultra pure waters, as well as within the pharmaceutical and chemical industries.
PP is a thermoplastic polymer made from polypropylene. It was first invented in the 1950s and has been used for pipes since the 1970s. Due to the high impact resistance combined with good stiffness and high chemical resistance makes this material suitable for sewer applications. A good performance at operating temperature range from up to 60 °C (140 °F) (continuous) makes this material suitable for in-house discharge systems for soil & waste. A special PP grade with high temperature behaviour up to 90 °C (194 °F) (short-term) makes that material a good choice for in-house warm water supply.
A PPR pipe is a form of plastic pipe made from a material known as polypropylene random copolymer plastic. The material is similar to that used in the manufacturing of water supply materials for household purposes, but it can be used to provide hot and cold drinking water as well as for heating systems. It was first launched in France in 1962 by its trade name ‘Plastic Pipe Revolvy.’
Since then, it has spread across Europe and other parts of the world. PPR pipes are becoming more popular because they save on energy costs when installed properly due to their sturdy build quality. They are also lighter than other piping options, which helps save on installation costs.
PPR pipes can be found in the following applications:
Water supply, sewage systems, gas supply (solvent-welded only), heat insulation, cold supply and cooling technology. Placing them underground is also possible due to their chemical resistance. PPR piping is commonly used within plumbing infrastructure for several reasons including its energy efficiency.
Besides that, it has a very long life span. It does not rust or corrode because of the material used, which is why it lasts so long, even when buried underground. The materials needed to build PPR pipes are readily available which makes them cheaper than other pipe materials such as copper.
A PPR pipe can hold its shape, which means it does not require a lot of space between joints, as would be the case with other pipes such as those made from PVC. In addition, it is not toxic, meaning it can be safely used in drinking water supply systems.
Main Uses of PPR Pipe Fittings
The most popular uses for Polypropylene (PPR) pipe fittings are in the transportation and handling of liquids. These applications usually consist of pumping or transferring fluids between containers such as tanks, drums, pails, jugs, kegs, etc. Pumps such as diaphragm pumps, peristaltic (rubber) tube pumps, and piston/plunger pumps are the types commonly used with polypropylene tubing to transport these fluid products. A few examples would be in dairy farms where the product is milk, in beverage industries handling beer products or malt beverages, and in commercial kitchens where salad dressings for salad bars are being kept cool.
Other uses of PPR Pipe Fittings include;
- Handling and distribution of compressed air, steam, and water. These applications usually consist of using diaphragm pumps, piston/plunger pumps, gear pumps, or peristaltic (rubber) tube pumps to move gasses or liquids through pipelines at various pressure head conditions.
Examples could be for compressed air in cylinders used by local shops like tire places or auto parts stores; water distribution systems where hot or cold potable water is used in homes; many types of farming; paper companies that use recycled water for paper making, cooling towers in large shopping malls or complexes where air conditioning is running throughout the building; aquariums that use pumps to circulate water through filters and aeration equipment.
- PPR pipe fittings are also used by many industries that require non-metallic piping components. One example would be dairy farms where milk products are being transferred between vehicles for distribution at stores, food chains, etc. Many of these pipes are located underground near hose bibs or animal waterers, so they cannot corrode or rust as steel piping systems do over time.
They can handle hot high temperatures up to 160 degrees F without warping because PPR pipe fittings meet FDA requirements for contact with consumable/edible food products. This is also true for non-potable applications of draining hot water tanks and heating systems.
- Toilet fill and flush valves in residential and commercial buildings where strict code compliance laws are being met to ensure easy cleaning of hard-to-reach areas around these valves without damage to ceramic surfaces or porcelain fixtures.
- Pumps, fluid lines, manifolds, etc. that are used in solar/saltwater pools systems for filtering pool waters through equipment that recycles the water back into the main pool body. These types of pools require components made specifically for saltwater exposure because salt will slowly corrode metals over time which can cause hazardous electrical wiring, pump wiring, etc.
- Fire suppression systems that require a polypropylene type material for tubing to carry gasses or liquids from tanks to nozzles or sprinklers throughout the building. PPR Pipe Fittings meet UL standards for this type of application and can be found in many major stadiums, commercial complexes, theaters, resorts, etc. where fire codes are strict because of the high occupancy factor during peak times.
- Lastly, PPR pipe fittings are also used by hobbyists who build different models such as RC cars (radio control) and planes to power pumps or compressors required for various operations like making custom tires or fuel cells needed to run engines efficiently.
What are the Advantages of PPR Pipes?
If you want a pipe that is corrosion-resistant, lightweight, and flexible but still has high durability, PPR could be the material you are looking for. Let us have a brief look at some of the major advantages of PPR pipes.
- Corrosion resistance: PPR pipes have a low corrosion rate in water environments or when exposed to weathering agents such as atmospheric oxygen and carbon dioxide. Compared with a steel pipe which corrodes roughly at 10-6~10-5mm/year in normal conditions, the corrosion rates of PPR pipes are between 10-11~10-9mm/year. The anticorrosive performance of products is good enough to make them last longer than metal materials under the same environmental condition.
- Lightweight: The density of most plastic materials is usually lower than that of water, but the density of PPR is even less than half that of water. This not only makes transportation conditions better but also reduces the workload during laying and lifting operations.
- Flexibility: Compared with metal pipes (such as iron/steel or copper), plastic pipe has good flexibility; it can be wrapped around corners without sharp angles or bends, which makes it easier to install.
- High durability: Plastic pipe made of PPR material used for underground piping systems can last longer than steel mainlines in an under-ground environment due to its corrosion resistance, lightweight and flexibility features. Unlike common perception, plastic pipes do not easily break when bent too sharply at a small angle within 180 degrees.
Main Feature of PPR Pipe System
1- With 20 °C and 25 ATM pressure, 50 year lifetime.
2- It is suitable among. 20 ° C and +95 ° C (freezing point of fluid in insulation must be considered)
3- It is durable due to these reasons.
4- High resistance to chemical substances.
5- Brilliant and smooth inner surface
6- The color, odor and taste of water do not change.
7- Provides heat and sound insulation.
8-There is no diameter twist on fittings. This provides maximum performance.
9- Up to 70% savings on installation and installation
10-Environmentally friendly
PB-1 (polybutylene)
PB-1 is used in pressure piping systems for hot and cold potable water, pre-insulated district heating networks, and surface heating and cooling systems. Key properties are weldability, temperature resistance, flexibility and high hydrostatic pressure resistance. One standard type, PB 125, has a minimum required strength (MRS) of 12.5 MPa. It also has low noise transmission, low linear thermal expansion, no corrosion and calcification.
PB-1 piping systems are no longer sold in North America. Market share in Europe and Asia is small but steadily growing. In some markets, e.g. Kuwait, UK, Korea and Spain, PB-1 has a strong position.
PVDF (Polyvinylidene Difluoride)
Polyvinylidene Difluoride (PVDF) is a fairly non-reactive, thermoplastic fluoropolymer with excellent chemical and thermal resistance for plastic pipework uses. PVDF resin is produced through polymerization of the vinylidene fluoride monomer. The PVDF resin is then used to make PVDF pipe as well as many other products.
Industries and applications select PVDF pipe due to its inert, durable qualities. PVDF piping is used most in the chemical process industry due to its ability to plumb aggressive, corrosive solutions. PVDF pipe also sees common use in high purity applications, semi-conductor fabrication, electronics / electricity, pharmaceutical developments, and nuclear waste processing.
PVDF piping specifications and performance characteristics approve PVDF pipe up to 248 °F (120 °C) under pressurized system conditions. The pipe does not support fungus growth according to military test standard method 508, 81-0B. Dissimilar from other common thermoplastic pipes, (uPVC, CPVC, PE, PP), PVDF does not exhibit sensitivity to UV light or ozone oxidative damage, approving it for long term outdoor uses.
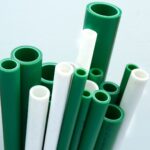
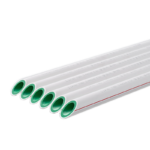
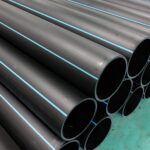
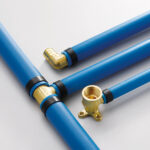
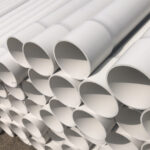
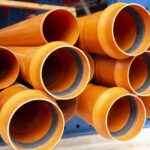
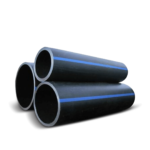
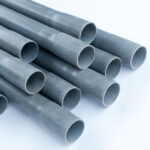