Boiler Tube
Other Boiler Tubes
1. Product introduction
Multi-Lead Rifled Seamless Tube is a seamless steel tube with thread-like channels rolled on the inner surface of the boiler evaporation heating surface.
The main materials of Multi-Lead Rifled Seamless Tube:
20G, SA-210 A1, SA-210 C, SA-213 T2, SA-213 T12, 12Cr1MoVG, 15CrMoG, SA-213 T22, SA-213 T23, SA213 T91 etc.
①SA210 A1(C) & SA213 T2 T12 multi-lead rifled seamless tube is suitable for the manufacture of power station boiler water wall, which can effectively eliminate the steam film on the inner wall of the steel pipe and improve the thermal efficiency of the furnace wall.
②SA210 A1(C) & SA213 T2 T12 multi-lead rifled seamless tube is manufactured by cold drawing method, so that the inner wall of the steel pipe forms a special geometrical inner wall spiral rib. The finished product adopts protective gas heat treatment, so that the steel pipe has stable performance and good surface quality.
③Multi-lead rifled seamless tube can be ordered according to user requirements.
Multi-Lead Rifled Seamless Tube Quick Details
Manufacture:Seamless process, cold drawn
Material (Grade): 20G, SA-210 A1, SA-210 C, SA-213 T2, SA-213 T12, 12Cr1MoVG, 15CrMoG, SA-213 T22, SA-213 T23,SA-213 T91 etc.
Wall thickness(WT): 2.8 mm-12.7 mm.
Outer diameter (OD): 23 mm-127 mm
Common specifications: Φ28.6×6.2, Φ38.1×7.5, Φ63.5×7.5, Φ66.7×8, etc.
Length: 6M or specified length as required.
Ends: Plain End, Beveled End, Treaded
Additional Info
Port of Shipment: Tianjin, China
Payment Terms: T / T, LC
Delivery: 7-15 days after payment
Surface: Tubes will be varnished (Outside only) to prevent rust.
Marking: Standard + Steel Grade + Size + Heat No + Lot No
Package: Bundles (hexagonal),Wooden Boxes,Crates (steel/wooden) or as required
2. Technical requirements of SA210 A1(C) & SA213 T2 T12 multi-lead rifled seamless tube
The multi-lead rifled seamless tube used for high-pressure boilers should not only meet the general requirements of smooth tubes, but also in accordance with the standard requirements of GB/T 20409-2006 “Multi-lead rifled seamless steel tube for high-pressure boilers” or the procurement specifications of each boiler manufacturer. There are different regulations for its size and thread parameter deviation.
Standard:
GB/T 20409-2018 multi-lead rifled seamless steel tube for high pressure boiler
3. the chemical composition of Multi-Lead Rifled Seamless Tube (%)
Material (Grade) | C | Mn | Si | Cr | Mo | S | P |
20G | 0.17~0.23 | 0.35~0.65 | 0.17~0.37 | — | — | ≤0.020 | ≤0.025 |
20MnG | 0.17~0.23 | 0.70~1.00 | 0.17~0.37 | — | — | ≤0.020 | ≤0.025 |
25MnG | 0.22~0.29 | 0.70~1.00 | 0.17~0.37 | — | — | ≤0.020 | ≤0.025 |
12CrMoG | 0.08~0.15 | 0.40~0.70 | 0.17~0.37 | 0.40~0.70 | 0.40~0.55 | ≤0.020 | ≤0.025 |
15CrMoG | 0.12~0.18 | 0.40~0.70 | 0.17~0.37 | 0.80~1.10 | 0.40~0.55 | ≤0.020 | ≤0.025 |
SA-210A1 | ≤0.27 | ≤0.93 | ≥0.10 | — | — | ≤0.035 | ≤0.035 |
SA-210C | ≤0.35 | 0.29~1.06 | ≥0.10 | — | — | ≤0.035 | ≤0.035 |
SA-213T2 | 0.10~0.20 | 0.30~0.61 | 0.10~0.30 | 0.50~0.81 | 0.44~0.65 | ≤0.025 | ≤0.025 |
SA-213T12 | 0.05~0.15 | 0.30~0.61 | ≤0.50 | 0.80~1.25 | 0.44~0.65 | ≤0.025 | ≤0.025 |
4.the mechanical properties of Multi-Lead Rifled Seamless Tube
Material (Grade) | Tensile strength (MPa) | Yield strength (MPa) | Elongation(%) | Hardness |
20G | 410~550 | 245 | ≥24 | — |
20MnG | ≥415 | ≥240 | ≥22 | — |
25MnG | ≥485 | ≥275 | ≥20 | — |
12CrMoG | 410~560 | ≥205 | ≥21 | — |
15CrMoG | 440~640 | ≥235 | ≥21 | — |
SA-210C | ≥415 | ≥255 | ≥30 | ≤143HBW |
SA-210A1 | ≥485 | ≥275 | ≥30 | ≤179HBW |
SA-213T2 | ≥415 | ≥205 | ≥30 | ≤163HBW |
SA-213T12 | ≥415 | ≥220 | ≥30 | ≤163HBW |
5. Heat treatment system of Multi-Lead Rifled Seamless Tube
Material (Grade) | Heat treatment |
20G | Normalizing at 900℃~930℃, the holding time is 1min/mm according to the wall thickness, but should not be less than 12min. |
20MnG | Normalizing at 900℃~930℃, the holding time is 1min/mm according to the wall thickness, but should not be less than 12min. |
25MnG | Normalizing at 900℃~930℃, the holding time is 1min/mm according to the wall thickness, but should not be less than 12min. |
12CrMoG | 900°C~930°C normalizing; 670°C~720°C tempering, holding time: Periodic furnace is more than 2h, continuous furnace is more than 1h. |
15CrMoG | Normalizing at 930°C~960°C; tempering at 680°C~720°C, holding time: periodic furnace greater than 2h, continuous furnace greater than 1h. |
Multi-Lead Rifled Seamless Tube (referred to as internal threaded tube) refers to a seamless steel tube whose inner wall is processed into spiral grooves.
At present, in the large-capacity subcritical and supercritical thermal power boilers of 300 MW, 600 MW and above designed by our country or imported from abroad, the membrane water wall generally adopts Multi-Lead Rifled Seamless Tube.
Multi-Lead Rifled Seamless Tube Compared with ordinary smooth tubes, Multi-Lead Rifled Seamless Tube can effectively prevent the formation of a vapor film between water and the pipe wall, increase the disturbance of the flow in the steel pipe, and make the temperature of the pipe wall more uniform. The steel pipe burns out, which improves the heat transfer efficiency of the boiler.
The thread number of Multi-Lead Rifled Seamless Tube can be 4, 6, 8, or 12 according to the needs.
EN 10088-2-2009 X6CrNiMoTi17-12-2 Titanium Austenitic Stainless Steel Pipe
1.4571 (X6CrNiMoTi17-12-2) belongs to the European standard titanium-containing austenitic stainless steel,
Executive standard: EN 10088-2-2009
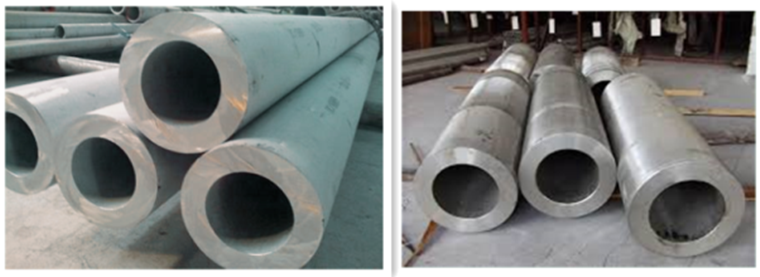
Equivalent grades of X6CrNiMoTi17-12-2 (1.4571)
Standard | Grade |
EU EN | X6CrNiMoTi17-12-2 |
USA | 316Ti |
Germany DIN,WNr | X10CrNiMoTi18-10 X6CrNiMoTi17-12-2 |
Japan JIS | 316Ti SUS316Ti |
France AFNOR | Z6CNDT17-12 Z6CNT17-12 |
England BS | 320S31 321S12 |
Italy UNI | X6CrNiMoTi17-12 |
China GB | 0Cr18Ni12Mo2Ti 1Cr18Ni12Mo2Ti |
Sweden SS | 2350 2350-02 |
Poland PN | H17N13M2T |
Czechia CSN | 17348 |
Finland SFS | 761 |
Austria ONORM | X6CrNiMoTi17-12-2S |
Russia GOST | 08KH17N13M2T 10KH17N13M2T |
Chemical composition of EN 10088-2-2009 X6CrNiMoTi17-12-2 (1.4571) Stainless Steel Pipe
Grades | Chemical composition(%) | ||||||||
C | Si | Mn | Ni | P | S | Cr | Mo | Ti | |
X6CrNiMoTi17-12-2 | ≤0.08 | ≤1.0 | ≤2.0 | 10.5 – 13.5 | ≤0.045 | ≤0.015 | 16.5 – 18.5 | 2.0 – 2.5 | 5 * C to 0.7 |
Note: Particular ranges of sulphur content may provide improvement of particular properties. For machinability a controlled sulphur content of 0.015 % to 0.030% is recommended and permitted. For weldability, a controlled sulphur content of 0.008 % to 0.030 % is recommended and permitted. For polishability, a controlled sulphur content of 0.015 % max is recommended. Elements not listed in this table shall not be intentionally added to the steel without the agreement of the purchaser except for finishing the cast. |
Mechanical properties of EN 10088-2-2009 X6CrNiMoTi17-12-2 (1.4571) Stainless Steel Pipe
Rm – Tensile strength (MPa) (+A) | 500-700 |
Rm – Tensile strength (MPa) (+AT) | 500-730 |
Rm – Tensile strength (MPa) (+AT+C) | 810-850 |
Rp0.2 0.2% proof strength (MPa) (+A) | 200-240 |
Rp0.2 0.2% proof strength (MPa) (+AT) | 190-210 |
KV – Impact energy (J) transverse, (+A) | +20° 60 | -196° 60 |
KV – Impact energy (J) longitud., (+A) | +20° 100 |
A – Min. elongation at fracture (%) (+A) | 30-40 |
A – Min. elongation at fracture (%) longitud., (+AT) | 35-45 |
Nominal diameter (mm): | 2 – 50 |
Z – Reduction in cross section on fracture (%) | 60-65 |
Brinell hardness (HB): (+A) | 215 |
Brinell hardness (HB): (+AT) | 210 |
Heat treatment of EN 10088-2-2009 X6CrNiMoTi17-12-2 (1.4571) Stainless Steel Pipe
Thermoforming temperature/℃ | Heat treatment temperature | Delivery status | High temperature yield strength/Mpa | ||||
Quenching | 100℃ | 200℃ | 300℃ | 400℃ | 500℃ | ||
1200-900 | 1020-1120,Air/water cooling | Solid solution | 185 | 165 | 145 | 135 | 129 |
Characteristics of X6CrNiMoTi17-12-2 Stainless Steel Pipe
Resistance to intergranular corrosion: in the delivery condition – yes; in the sensitized condition – yes.
1.4571 (X6CrNiMoTi17-12-2) Steel shal not be applied at a metal temperature lower than -196 ° C
Application
1.4571 (X6CrNiMoTi17-12-2) steel is added with Ti to improve the resistance to intergranular corrosion. Used in equipment resistant to sulfuric acid, phosphoric acid, and acetic acid.
Stainless Steel Corrugated Tube is usually used in heat exchange equipment. Compared with ordinary seamless steel pipes, Stainless Steel Corrugated Tube has a larger heat exchange area, smaller tube wall thermal resistance, and excellent heat transfer coefficient, so it is not Stainless Steel Corrugated Tube For Heat Exchanger is a new type of high-efficiency heat exchange tube that replaces the tube and has been widely used in heat exchange equipment.
Stainless Steel Corrugated Tube For Heat Exchanger is a thin-walled tube with large and small arcs continuously tangent and corrugated inside and outside. The three-dimensional movement outside the tube, so the degree of disturbance is more intense, even if the fluid flow rate is very low, it can make it into a turbulent state, and at the same time, the thin tube wall has a small temperature gradient, which greatly reduces the thermal resistance of the tube wall and improves the heat transfer inside and outside the tube. Coefficient, so that the overall heat transfer coefficient is improved.
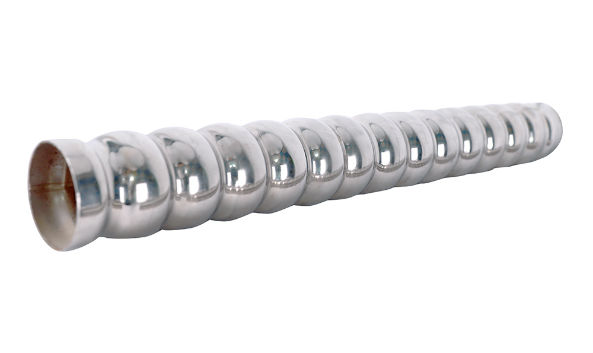
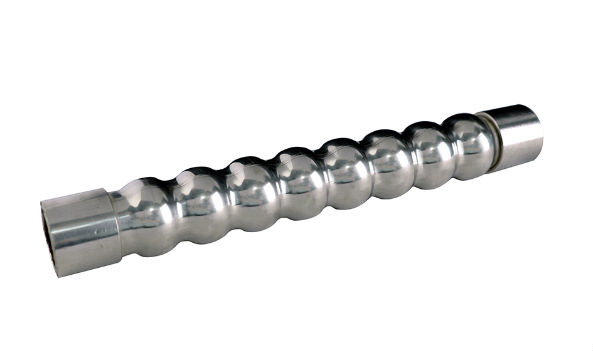
1.The Main Material(Grade)
TP304, TP304L, TP321, TP316, TP316L, TP310S, TP347H, 2205, 2507, TP904L
Chemical composition of Stainless Steel Corrugated Tube
Grade | Chemical composition, % | |||||||||||
C | S | Mn | P | S | Cr | Ni | Nb | Mo | Cu | N | Other | |
Max | ||||||||||||
TP304 | 0.08 | 1.00 | 2.00 | 0.045 | 0.03 | 18-20 | 8-11 | |||||
TP304L | 0.035 | 1.00 | 2.0 | 0.045 | 0.03 | 18-20 | 8-13 | — | — | — | — | |
TP321 | 0.08 | 0.75 | 2.00 | 0.045 | 0.03 | 17-19 | 9-12 | Ti= 5(C+N) 0.70 | ||||
TP316 | ≤0.08 | 0.75 | 2.00 | 0.045 | 0.03 | 16-18 | 10-14 | 2.0-3.0 | ≤0.10 | |||
TP316L | 0.04-0.10 | 1.00 | 2.00 | 0.045 | 0.03 | 16-18 | 11-14 | — | 2.0-3.0 | — | — | |
TP310S | 0.08 | 1.00 | 2.00 | 0.045 | 0.03 | 24-26 | 19-22 | — | ≤0.75 | — | — | |
TP347H | 0.04-0.10 | 1.00 | 2.00 | 0.045 | 0.03 | 17-19 | 9-13 | 8*C-1.1 | ||||
S32205 | 0.030 | 1.0 | 2.0 | 0.03 | 0.02 | 22-23 | 4.5-6.5 | — | 3.0-3.5 | — | 0.14-0.2 | |
TP904L | 0.02 | 1.00 | 2.00 | 0.045 | 0.035 | 19~23 | 23~28 | — | 4.0~5.0 | 1.0~2.0 | — |
Small outer diameter mm | Large outer diameter mm | Crest distance mm | Weightkg/m | Heat exchange area m2/m | |||||||
0.6 | 0.7 | 0.8 | 0.9 | 1.0 | 1.1 | 1.2 | 1.5 | ||||
16 | 19 | 15 | 0.257 | 0.297 | 0.336 | 0.375 | 0.414 | 0.437 | 0.0572 | ||
18 | 22 | 15 | 0.292 | 0.338 | 0.383 | 0.427 | 0.471 | 0.515 | 0.542 | 0.0665 | |
18 | 22 | 20 | 0.291 | 0.336 | 0.380 | 0.425 | 0.468 | 0.512 | 0.537 | 0.0658 | |
19 | 22 | 20 | 0.306 | 0.357 | 0.394 | 0.439 | 0.485 | 0.531 | 0.576 | 0.0665 | |
19 | 25 | 20 | 0.318 | 0.367 | 0.416 | 0.465 | 0.514 | 0.0747 | |||
20 | 25 | 20 | 0.332 | 0.383 | 0.436 | 0.485 | 0.535 | 0.585 | 0.635 | 0.0750 | |
22 | 25 | 20 | 0.351 | 0.406 | 0.461 | 0.513 | 0.568 | 0.622 | 0.672 | 0.0759 | |
25 | 28 | 25 | 0.399 | 0.463 | 0.526 | 0.588 | 0.649 | 0.711 | 0.771 | 0.952 | 0.0852 |
25 | 30 | 25 | 0.408 | 0.471 | 0.536 | 0.600 | 0.665 | 0.727 | 0.789 | 0.974 | 0.0902 |
25 | 32 | 25 | 0.426 | 0.487 | 0.555 | 0.622 | 0.685 | 0.751 | 0.814 | 0.0957 | |
27 | 30 | 25 | 0.440 | 0.510 | 0.576 | 0.645 | 0.714 | 0.778 | 0.846 | 1.045 | 0.0916 |
27 | 32 | 25 | 0.445 | 0.516 | 0.586 | 0.654 | 0.722 | 0.790 | 0.858 | 1.060 | 0.0966 |
32 | 38 | 30 | 0.527 | 0.610 | 0.691 | 0.774 | 0.850 | 0.929 | 1.007 | 1.247 | 0.1144 |
32 | 40 | 30 | 0.537 | 0.624 | 0.710 | 0.796 | 0.880 | 0.965 | 1.049 | 0.1198 | |
32 | 42 | 30 | 0.562 | 0.650 | 0.733 | 0.812 | 0.888 | 0.974 | 1.059 | 0.1258 | |
38 | 42 | 35 | 0.616 | 0.713 | 0.811 | 0.908 | 1.002 | 1.099 | 1.192 | 0.1275 | |
38 | 45 | 40 | 0.631 | 0.732 | 0.833 | 0.931 | 1.025 | 1.123 | 1.217 | 0.1336 | |
40 | 50 | 45 | 0.883 | 0.970 | 1.074 | 1.179 | 1.283 | 0.1480 | |||
48 | 54 | 50 | 1.151 | 1.276 | 1.401 | 0.1653 | |||||
50 | 57 | 50 | 1.282 | 1.487 | 1.532 | 1.892 | 0.1682 | ||||
50 | 62 | 50 | 1.367 | 1.501 | 0.1861 |
Note: Other specifications can also be produced by agreement.
3.Maximum allowable working pressure of stainless steel corrugated tube
Grade | Specification | Temperature ℃ | |||||||
Nodal peak outer diameter | Wall thickness | ≤20 | 100 | 150 | 200 | 250 | 300 | 350 | |
Allowable pressure Mpa | |||||||||
0Cr18Ni9 0Cr18Ni10Ti 0Cr17Ni12Mo2 0Cr19Ni13Mo3 | 32/45 | 0.6 | 2.6/1.9 | 2.4/1.8 | 3.7/1.7 | 2.1/1.6 | 2.1/1.6 | ||
0.7 | 3.0/2.3 | 2.9/2.1 | 2.7/2.0 | 2.5/1.8 | 2.4/1.8 | ||||
0.8 | 3.4/2.6 | 3.3/2.5 | 3.1/2.3 | 2.9/2.2 | 2.8/2.1 | ||||
0.9 | 3.9/2.9 | 3.7/2.8 | 3.5/2.6 | 3.2/2.4 | 3.2/2.4 | ||||
1.0 | 4.3/3.3 | 4.1/3.1 | 3.9/2.9 | 3.6/2.7 | 3.5/2.6 | ||||
1.1 | -/3.6 | -/3.4 | -/3.2 | -/3.0 | -/2.9 | ||||
1.2 | -/3.9 | -/3.7 | -/3.5 | -/3.3 | -/3.2 | ||||
00Cr19Ni10 00Cr17Ni14Mo2 00Cr19Ni13Mo3 | 0.6 | 2.4/1.8 | 2.2/1.6 | 2.0/1.5 | 1.9/1.4 | 1.8/1.4 | |||
0.7 | 2.8/2.1 | 2.5/1.9 | 2.4/1.8 | 2.2/1.7 | 2.1/1.6 | ||||
0.8 | 3.2/2.4 | 2.9/2.2 | 2.7/2.0 | 2.6/1.9 | 2.4/1.8 | ||||
0.9 | 3.6/2.7 | 3.3/2.5 | 3.0/2.3 | 2.9/2.2 | 2.7/2.1 | ||||
1.0 | 4.0/3.0 | 3.7/2.8 | 3.4/2.5 | 3.2/2.4 | 3.1/2.3 | ||||
1.1 | -/3.3 | -/3.0 | -/2.8 | -/2.7 | -/2.5 | ||||
1.2 | -/3.6 | -/3.3 | -/3.1 | -/2.9 | -/2.8 |
Note:
1. The blasting pressure safety factor is 8;
2. The allowable pressure of the intermediate temperature can be obtained by interpolation according to the pressure value of this table;
3. The front side of the diagonal line is the allowable pressure value of Φ32 series (including Φ19, Φ22, Φ25, Φ32), and the back of the allowable pressure value of Φ45 series (including Φ38, Φ40, Φ42, Φ44, Φ45).
4.Process flow chart of Stainless Steel Corrugated Tube For Heat Exchanger
5.Stainless Steel Corrugated Tube For Heat Exchanger has the following advantages.
(1)The uneven surface of Stainless Steel Corrugated Tube makes the fluid form strong turbulence in the tube, thereby greatly improving the heat transfer coefficient of the inner and outer surfaces of the tube, and the overall heat transfer efficiency of the heat exchanger is increased by 2-3 times than that of the tube type;
(2)Stainless Steel Corrugated Tube is resistant to high temperature and can withstand large temperature and pressure differences
Although the wall of the Stainless Steel Corrugated Tube is very thin (0.6-1.2mm), the special free forming process and unique arc shape greatly improve its pressure-bearing capacity. At the same time, the corrugated tube heat exchanger can adapt to a higher working temperature, up to 350°C. Corrugated pipe is a kind of flexible element with certain thermal compensation ability, good adaptability to large working temperature difference, small thermal stress of equipment, and obvious superiority over ordinary seamless steel pipe.
(3)The corrugated tube has a self-cleaning effect through thermal expansion and contraction, has the performance of not easy to scale, and compensates for the thermal stress caused by the temperature difference;
Heat exchanger fouling, corrosion and blockage have always been a difficult problem to solve, especially when the water quality is poor, the water treatment effect is not good, the gas medium contains impurities or chemical reactions are prone to form fouling substances. The problem is particularly prominent. In the lighter case, the function of the heat exchanger decreases, the working condition deteriorates, the resistance becomes larger, and the energy consumption increases, while the worst case is that the heat exchanger is blocked and cannot operate, so the workload of maintenance, cleaning or renewal of the heat exchanger will also increase. Therefore, the use of Stainless Steel Corrugated Tubes for the tube bundle in the heat exchanger will completely solve this problem.
(4)Due to the compensation function of the Stainless Steel Corrugated Tube, the thermal stress of the tube sheet can be reduced, the tube opening will not be broken and the leakage problem will be caused, and the heat exchanger is safe and durable;
In addition to the above advantages, the corrugated tube produced by Dongyan Energy Conservation has the advantages of strong corrosion resistance, longer life, no pitting, and low price.
(5)Stainless steel corrugated pipe has uniform stress distribution and strong corrosion resistance
Because the stainless steel corrugated tube adopts a unique forming process, the feature of this process is that during the forming process, the deformation is not formed by the forced flow of metal in the mold, but a free-flowing “soft forming” process. Because there is no forced deformation, the forming process will not cause stress concentration, small residual stress, uniform stress distribution, no intercrystalline defects, and strong stress corrosion resistance.
(6)The stainless steel corrugated tube has a long service life and high cost performance.
The corrugated pipe adopts ultra-thin stainless steel material, which on the one hand improves the service life of the product, but also greatly reduces the weight of the product, saves materials, reduces the cost of operation and maintenance, reduces the floor space, and greatly improves the cost-effectiveness of the product. The economic benefits are obvious.
6.Application
Stainless Steel Corrugated Tube For Heat Exchanger has now been widely used in petroleum, chemical industry, power system, heating and heating, etc.
Boiler Tubes Erosion Shields, also known as anti-corrosion Shields, anti-wear plate, anti-wear protection Shields, anti-wear cover plate, anti-corrosion cover plate, boiler climbing pipe, anti-wear pressure plate, etc. , which are used in combination with snap rings.
Boiler Tubes Erosion Shields are produced using a high-pressure press and professional mold pressing. The production time is short, the welding performance is good, the welding should not fall off, the surface is smooth, and the appearance is beautiful. Boiler Tubes Erosion Shields with bends are formed by pressing on a press or bending with a special abrasive on a tube bender.
1.Application
Boiler Tubes Erosion Shields are mainly used on the windward side of the heating surface of the boiler, such as superheaters, reheaters, economizers, and water-cooled wall pipes. The main role is to protect the heating surface of the boiler pipes, reduce pipeline wear, and increase the heating surface of the pipes. Service life. In general, most of them are called “wear-resistant tile” and “wear-resistant cover plate”. Erosion Shields are special boiler accessories. Generally, most of them are used in power station boilers, small boilers are used less, and some coal chemical industries will also use them.
2.Material
Different types of stainless steel are selected according to the specific conditions of different working conditions. Common materials are: TP321 (Cr18Ni9Ti), TP309S (Cr23Ni13), 1Cr20Ni14Si2, TP310S (Cr25Ni20), 1Cr25Ni20Si2, and some low temperature areas (such as low temperature superheater, low temperature reheater) are made of 1Cr13, 1Cr6Si2Mo and other materials. The boiler was originally designed to be accurate. Different materials have different temperature resistance and mechanical strength. 1Cr13, 1Cr6Si2Mo generally has a temperature resistance of 600 ℃ or less.
Material(Grade) | Temperature resistance | Yield strength | Tensile strength | Elongation | HB | HRB | HV |
1Cr18Ni9Ti | 925 ℃ | ≥205MPa | ≥520MPa | ≥40% | ≤187 | ≤90 | ≤200 |
Cr23Ni13 | 1095 ℃ | ≥205MPa | ≥520MPa | ≥40% | ≤187 | ≤90 | ≤200 |
1Cr20Ni14Si2 | 1095 ℃ | — | ≥590MPa | ≥40% | — | — | — |
Cr25Ni20 | 1150 ℃ | ≥205MPa | ≥520MPa | ≥40% | ≤187 | ≤90 | ≤200 |
1Cr25Ni20Si2 | 1150 ℃ | — | ≥540MPa | ≥35% | — | — | — |
We can also supply Boiler Tubes Erosion Shields of other materials.
3.Specifications
Processing thickness of Boiler Tubes Erosion Shields
Boiler Tubes Erosion Shields are processed in thicknesses of 2mm, 3mm, 4mm, and 5mm. Different thickness is adopted according to the wear severity and the need of heat conduction.
Shapes and specifications of Boiler Tubes Erosion Shields
The cross-sectional shape of Boiler Tubes Erosion Shields is mostly semi-circular (180 degrees), and there are also 120-160 degrees. It is mainly used on finned tubes (water-cooled walls); Boiler Tubes Erosion Shields are divided into direct wear-resistant shields, In-curve anti-wear shields, outer-curve anti-wear shields, side-curve anti-wear shields, S-curve anti-wear shields, etc. The length of the straight anti-wear shields ranges from 20mm to 3000mm, and the general length of 1000-2000mm is commonly used. The anti-wear shields with bends generally requires a processing drawing and the following parameters should be on the drawing: outer diameter of the pipe used, bending of the pipe Radius R (to the center of the pipe), the degree of bending angle, and the length of the straight sections on both sides of the arc segment of the wear-resistant shields.
The most basic parameter of Boiler Tubes Erosion Shields is the outer diameter of the tube used (that is, the inner diameter of Boiler Tubes Erosion Shields). The main specifications of the tube are: 32, 38, 42, 44.5, 48, 51, 57, 60, 63.5 , 76, 89mm, etc .; The inner diameter of the Boiler Tubes Erosion Shields is usually 1-3mm larger than the outer diameter of the tube used, depending on the actual requirements.
4.Accessories: Snap rings
Snap rings .: Used in conjunction with Boiler Tubes Erosion Shields, which is a clip that easily installs Boiler Tubes Erosion Shields to the tube. The snap ring and Boiler Tubes Erosion Shields are overlapped and welded, generally about 190-200 degrees Erosion Shields is a 180-degree semicircle), but also leave a welding position for easy welding and fixing. Generally, each piece of Boiler Tubes Erosion Shields needs to be equipped with 2-4 snap rings with a pitch of 200-500mm.
Knowledge:
The service life of Boiler Tubes Erosion Shields is different in different types of boilers and different use parts. The normal service life is a period of overhaul (3-5 years) for the boiler. Generally, some boilers will be replaced or retrofitted every time the boiler is overhauled. The main replacements are those of the Boiler Tubes Erosion Shields that are severely thinned and exceeded the standard; those that were not firmly detached during the boiler operation during the previous installation. According to the wear of the Boiler Tubes Erosion Shields during replacement, if the thickness is severely reduced, it needs to be replaced, the deformation is severe, and those that cannot protect the tube also need to be replaced. In addition, some boiler tubes are not equipped with Boiler Tubes Erosion Shields, but during the boiler inspection, it is found that the tubes have a tendency of wear and thinning. Generally, Boiler Tubes Erosion Shields are also installed to prevent further wear of the tubes and cause serious consequences such as boiler explosion.
On the heating surface of superheater and economizer tube bundle of the boiler, in order to prevent the pipe from being worn by high temperature flue gas washing, boiler tubes erosion shields are mostly arranged on the outer side of the pipe in the direction of flue gas flow. The elbow erosion shields solves the abrasion problems of water wall tubes, superheater tubes, economizer tubes and reheater tubes in the furnace, and provides guarantee for the long-term and reliable operation of CFB boiler. With the increase of CFB boiler products, the type and quantity of The elbow erosion shields will increase.
Corten steel, divided into two categories: corten A and corten B, is the representative steel of U.S. Cu-P series, belonging to low alloy, high strength and atmospheric corrosion-resistant structural steel
Equivalents Grades
Corten | EN 10025-5:2004 | ASTM A588 | ASTM A242 |
Corten A | S355 J0WP | Grade A | Type 2 |
Corten A Seamless Steel Pipe
Corten A seamless steel pipes have excellent resistance to sulfur ion, hydrochloric acid and other acid corrosion.
Application
Corten A seamless steel pipes are mainly used for gas saving, air preheater, heat exchanger and evaporator in sulfur-containing flue gas to resist condensation corrosion of sulfur-containing flue gas.
Corten A Seamless Steel Pipee Quick Details
Standard:GB/T8162-2008
Manufacture:Seamless process
Wall thickness(WT): 1.5mm——19.0 mm.
Outer diameter (OD): 21.0 mm——219.0mm
Common specifications:40mm*1.5mm, 50mm*2.0mm, 57mm*2.0mm, 57mm*3.0, etc
Length: 6M or specified length as required.
Additional Info
Port of Shipment: Tianjin, China
Payment Terms:T / T, LC
Delivery: 7-15 days after payment
Surface: Tubes will be varnished (Outside only) to prevent rust.
Marking: Standard + Steel Grade + Size + Heat No + Lot No
Package: Bundles (hexagonal),Wooden Boxes,Crates (steel/wooden) or as required
Corten A Seamless Steel Pipe – Chemical Composition
Grade | C | Si | Mn | P | S |
Corten A | ≤0.12 | 0.25-0.75 | 0.20-0.50 | 0.07-0.15 | ≤0.03 |
Al | Cu | Cr | Ni | V | |
0.015-0.06 | 0.25-0.55 | 0.50-1.25 | ≤0.65 | – |
Corten A Seamless Steel Pipe – Mechanical Properties
Grade | Yield Strength Rel N/mm² | Tensile Strength Rm N/mm² | Elongation % |
Corten A | ≥355 | 470~630 | ≥20 |
Tolerances
Steel pipe | Outer diameter (OD) | wall thickness(WT) | ||
Cold drawn pipe | Outer diameter(mm) | tolerance | wall thickness(mm) | tolerance |
>30~50 | ±0.3 | ≤30 | ±5% | |
>50~219 | ±0.8% | |||
Hot rolled pipe | >219 | ±1.0% | >20 | ±5% |
253MA (S30815) high-temperature stainless steel tubes Quick Details
Type:seamless ,electric resistance welding process
Technique: Hot rolled or cold drawn
Standard:SA213, SA312
Outside Diameter :25mm-508mm
Wall thickness:6mm-22.8mm
Length:6000mm、12000m or specified length as required.
Type of End-Finish:Plain End、Beveled End、Treaded
Surface treatment: Tubes will be varnished (Outside only) to prevent rust.
Additional Info
Payment Terms:T / T, LC
Port of Shipment:Tianjin,China
Package:According To Per Customers’ Require
Marking:Standard + Steel Grade + Size + Heat No + Lot No
Delivery time:Tubes will be completed within 30 days, and urgent delivery time can be discussed.
Heat Treatment
Solution Treatment (Annealing) Heat to 1050-1150°C and cool rapidly. It is recommended that the material be solution treated after 10-20% cold work to achieve maximum creep strength in service.
253MA (S30815) high-temperature stainless steel tube cannot be hardened by thermal treatment.
Manufacture
253MA (S30815) high-temperature stainless steel tubes are manufactured by seamless process or by electric resistance welding process
253MA (S30815) high-temperature Stainless steel tube is readily fabricated by standard commercial procedures. In comparison to carbon steel, stainless steels are tougher and tend to work harden rapidly. However, with positive feeds and slow speeds combined with abundant cutting fluid this alloys tendency to work harden may be minimized.
253MA (S30815) high-temperature Stainless steel tube can be welded using conventional welding processes. Filler metal should be of similar composition for maximum weld integrity and properties
Chemical Composition of 253MA (S30815) high-temperature stainless steel tubes , %
Grade | Chemical Composition | ||||||||
253 MA | Cr | Ni | C | Si | Mn | P | S | N | Ce |
20.0-22.0 | 10.0-12.0 | 0.05-0.10 | 1.40-2.00 | 0.80max | 0.040max | 0.030max | 0.14-0.20 | 0.03-0.08 |
Mechanical Properties Room Temperature
Specified Limits Minimum | Typical Range | |
Ultimate Tensile Strength, psi | 87,000 | 90,000-114,000 |
.2% Offset Yield Strength, psi | 45,000 | 45,000-69,000 |
Elongation in 2″, % | 40 | 42-70 |
Reduction of Area, % | 50 | – |
Hardness Rockwell B | – | Rb 90 |
The chemical composition of the 253MA (S30815) high-temperature stainless steel tube is balanced, which makes the 253MA (S30815) stainless steel tube have the most suitable comprehensive performance in the temperature range of 850 °C-1100 °C, high oxidation resistance, and the scale temperature is up to 1150 °C; extremely high creep resistance Variability and creep rupture strength; good resistance to high temperature corrosion and resistance to brush corrosion in most gaseous media; high yield strength and tensile strength at high temperatures; good formability and Solderability and sufficient machinability.
In addition to the alloying elements chromium and nickel, the 253MA (S30815) high-temperature stainless steel tube also contains a small amount of rare earth metal, which significantly improves its antioxidant capacity. Nitrogen is added to improve creep properties and make this steel tube a complete austenite. Although the chromium and nickel contents are relatively low, this stainless steel tube has many of the same high temperature characteristics as the high alloyed alloy steel tube and the nickel base alloy steel tube.
Application:
253MA (S30815) high-temperature stainless steel tubes are widely used in sintering equipment, blast furnace equipment, steel melting, furnaces and continuous casting equipment, rolling mills (heating furnaces), heat treatment furnaces and accessories, mineral equipment and cement production equipment.
The 253MA (S30815) high-temperature stainless steel tube can be used at pressures up to 900 °C and non-pressured high temperature parts with operating temperatures up to 1150 °C.
254 SMO stainless steel tube is an austenitic stainless steel tube. Due to its high molybdenum content, it has extremely high pitting and crevice corrosion resistance. The 254 SMO stainless steel tube was developed and developed for use in halide-containing environments such as seawater. 254SMO is the 1978 patent steel number of Avesta, Sweden
The 254 SMO stainless steel tube has good resistance to uniform corrosion. Especially in halide-containing acids, the steel is superior to ordinary stainless steel. Its C contains <0.03%, so it is called pure austenitic stainless steel tube.
Manufacturing process
Since the 254S MO stainless steel tube is a high-alloy material, it is quite complicated in the manufacturing process. Generally, people can only rely on traditional techniques to manufacture such special stainless steel tubes, such asseamless, pouring, forging, calendering and the like.
Heat treatment
If additional heat treatment is needed due to further processing the following is recommended.
Solution annealing
1150–1200°C (2100–2190°F), quenching in water. Thin-walled tubes min. 1130°C (2060°F), quenching in air/water.
National standards:
UNS S31254, DIN/EN 1.4547, ASTM A280, ASME SA-240
Matching welding consumables:
ERNiCrMo-3 welding wire, ENiCrMo-3 welding rod
Chemical composition (nominal) %
Standards | Grade | C | Si | Mn | P |
Outokumpu | 254 SMO | ≤0.020 | ≤0.80 | ≤1.00 | ≤0.030 |
ASTM A182 | F44 S31254 | ≤0.020 | ≤0.80 | ≤1.00 | ≤0.030 |
DIN EN 10088-3-2005 | X1CrNiMoN20-18-7 1.4547 | ≤0.020 | ≤0.70 | ≤1.00 | ≤0.030 |
S | Cr | Ni | Mo | N | Cu |
≤0.010 | 19.5-20.5 | 17.5-18.5 | 6.0-6.5 | 0.18-0.22 | 0.5-1.0 |
≤0.010 | 19.5-20.5 | 17.5-18.5 | 6.0-6.5 | 0.18-0.22 | 0.5-1.0 |
≤0.010 | 19.5-20.5 | 17.5-18.5 | 6.0-7.0 | 0.18-0.25 | 0.5-1.0 |
Mechanical properties
Standards | Grade | Tensile strength | Yield strength | Elongation | Hardness |
Outokumpu | 254 SMO | ≥650 MPa | ≥300 MPa | ≥ 35% | ≤96 HRB |
Features of 254SMO stainless steel tube
1. 254SMO stainless steel pipes also have high crevice corrosion resistance in seawater, and only a few types of stainless steel pipes have this property.
2. The corrosion resistance of 254SMO stainless steel tubes in acidic solutions and oxidizing halide solutions such as paper bleaching can be compared to nickel-based alloys and titanium alloys with the strongest corrosion resistance.
3. Since the 254SMO stainless steel tube has a high nitrogen content, its mechanical strength is higher than other types of austenitic stainless steel tubes. In addition, the 254SMO stainless steel tube also has high ductility and impact strength as well as good weldability.
4. The high molybdenum content of the 254SMO stainless steel tube allows it to have a higher oxidation rate during annealing, resulting in a rougher surface than the normal stainless steel tube after pickling. However, this has no adverse effect on the corrosion resistance of the steel.
Application areas of 254SMO stainless steel pipe:
1. Ocean: marine structures in the sea environment, seawater desalination, marine aquaculture, seawater heat exchange, etc.
2. Environmental protection field: flue gas desulfurization device for thermal power generation, wastewater treatment, etc.
3. Energy field: atomic power generation, comprehensive utilization of coal, and ocean wave power generation.
4. Petrochemical industry: refining, chemical and chemical equipment.
5. Food field: salt making, soy sauce brewing, etc.
6. High concentration chloride ion environment: paper industry, various bleaching devices
Alloy Steel U-tube heat exchanger tubes are bent into a U-shaped tube, the fluid inlet and outlet were installed in the same side on both sides of the head with partitions into two rooms, each tube is free to expand and retract to solve the heat Compensation problem.
The U tube is an important part of the U tube heat exchanger.
The main structure of the U type tube heat exchanger includes the tube box, the barrel, the head, the heat exchange tube, the nozzle, the baffle plate, the punching plate and the guide tube, the short circuit structure, the support and other accessories.
Alloy Steel U tubes used for heat transfer tubes is usually used for heat transfer tubes and ordinary cold drawn tubes. The former is suitable for non phase transition heat transfer and vibration prone situations, and the latter is suitable for reboiling, condensing heat transfer and non vibration general situations.
Alloy Steel U tubes has a variety of forms, smooth tube is the most traditional form, because it has the advantages of easy manufacturing and low unit length cost, which is the most common in the current application. The pipe should be able to withstand certain temperature and stress. When the tube and shell side fluid are corrosive, the pipe should also have corrosion resistance.
The material of Alloy Steel U tubes:T5, T11, T12, T22, T9, T91, etc.
Alloy Steel U Tube Quick Details
Size Range:OD 5/8″~1 1/2″ ,
WT :1.65mm~2.77mm
Min Radio: 29mm ;
Max Radio:675.84mm
Payment:L/C or T/T
Delivery: 7-15 days after payment
Type of End-Finish:PE
Tchnical conditions:
Heat treatment:Stress relive annealing of U-tubes after bending
Surface condition Finished U-tubes shall be free of scale, without scratches after bending
Dimensional tolerances U-tubes acc. to TEMA R.C.B.
Length of straight part -0/+5 mm
Flattening (also called “ovality”) at the bend shall not exceed 10% of the nominal tube outside diameter.
Wall thickness in bending part acc. to TEMA RCB 2.31
Minimum tube wall thickness in the bend part (T min)
T(min) ≥ (SW × (2×R + D))/( 2× (R+D)
where: SW is smallest wall thickness
D Nominal outside diameter
Rradius
Radius tolerance
1) for R 100 mm +/- 3 mm
2) for R ≥ 100 mm +/- 5 mm
Straightness tolerance max. 1,5 mm per 1 m
U-Tube ends: plain, vertically cut to the tube axis
Repairs by welding: prohibited
Surface condition Finished U-tubes shall be free of scale, without scratches after bending,
Mandatory tests for U-tubes
100 % Dimensional and visual control.
100 % Ball passed test
100 % Hydrostatic test min 10Mpa/ min 10sec.
Coating :Passivation and oiled, Black paint or varnish
Packing:Plastic plugs in both ends, bundles of max. 3,000kg with several steel strips, Two tags on each bundle, Wrapped in waterproof paper packed in wooden case
Mill Test Certificate:EN 10204/3.1B
Types of Packaging:
– Special crates for U-Bend tubes with each radius separated
– Our Heat Exchanger Alloy Steel U Tube packing can meet any needs of the customers.
Delivery: 7-15 days after payment
The U tube heat exchanger has only one tube plate, both ends of the tube are fixed on the same tube plate. The tube can expand freely, have no thermal stress, and have good heat compensation performance. The tube process adopts a double pipe range, the flow rate is long, the flow velocity is high, the heat transfer performance is good, the pressure bearing capacity is strong, the tube bundle can be pulled out of the shell, easy to repair and clean and structure. Simple and cheap.
Stainless Steel U-tube heat exchanger tubes are bent into a U-shaped tube, the fluid inlet and outlet were installed in the same side on both sides of the head with partitions into two rooms, each tube is free to expand and retract to solve the heat Compensation problem.
Heat Exchanger Stainless Steel U Tube Typical Grade: SS 410, 410S, 430, 439, 446, 444, 440C, L80 / 13Cr etc.
Heat Exchanger Stainless Steel U Tube Quick Details
Company Name: beite steel pipe
Country/Region: China
Product Name:Heat Exchanger Stainless Steel U Tube
Payment:L/C or T/T
Delivery: 7-15 days after payment
Type of End-Finish:PE
Package:Standard export package,suit for all kinds of transport, or as required
Certificate:ISO 9001-2000,PED 97/23/EC,ASME,DNV
Tchnical conditions:Heat treatment,Stress relive annealing of U-tubes after bendingSurface condition Finished U-tubes shall be free of scale, without scratches after bendin
Heat Exchanger Stainless Steel U Tube Dimensional Range & Specification
Size Range:OD 5/8″~1 1/2″ ,
WT 1.65mm~2.77mm
Min Radio: 29mm ;
Max Radio:675.84mm
Mandatory tests for Heat Exchanger Stainless Steel U Tube
1.100 % Dimensional and visual control.
2.100 % Ball passed test
3.100 % Hydrostatic test min 10Mpa/ min 10sec.
4.Coating :Passivation and oiled, Black paint or varnish
5.Mill Test Certificate:EN 10204/3.1B
Heat Exchanger Stainless Steel U Tube Packaging & Delivery
Types of Packaging:
– Bundles (hexagonal)
– Wooden Boxes
– Crates (steel/wooden)
– Special crates for U-Bend tubes with each radius separated
– Our Heat Exchanger Stainless Steel U Tube packing can meet any needs of the customers.
Delivery: 7-15 days after payment
SUS440C high hardness stainless steel pipe belongs to martensitic stainless steel pipe, and all stainless steel pipe and heat resistant steel pipe have the highest hardness (can reach HRC58 or above), and are mostly used for parts such as molds with corrosion resistance and hardness requirements.
SUS440C high hardness stainless steel tube Quick Details
Type:seamless steel tube
Outside Diameter :25mm-219mm
Wall thickness:6mm-15.8mm
Length:6000mm、12000m or specified length as required.
Type of End-Finish:Plain End、Beveled End、Treaded
Surface treatment: Tubes will be varnished (Outside only) to prevent rust.
Additional Info
Payment Terms:T / T, LC
Package:According To Per Customers’ Require
Marking:Standard + Steel Grade + Size + Heat No + Lot No
Delivery time:Tubes will be completed within 30 days, and urgent delivery time can be discussed.
Manufacture
SUS440C high hardness stainless steel tube are manufactured by seamless process.
Heat treatment:
1) Annealing, slow cooling at 800-900 ° C;
2) quenching, oil cooling at 1000~1050 °C;
3) Tempering, air cooling at 200 ~ 300 °C.
Metallographic organization: The tissue is characterized by martensite type.
Chemical Composition of SUS440C
Grade | Chemical Composition | ||||||
C | Si | Mn | P | S | Cr | Mo | |
SUS440C | 0.95-1.20 | ≤1.00 | ≤1.00 | ≤0.040 | ≤0.030 | 16.0-18.0 | ≤0.75 |
Grade | Mechanical Properties | |||
Tensile Strength | Yield Strength | Elongation | Hardness | |
Mechanical Properties | 560Mpa | 250Mpa | 18% | 250 |
Characteristics of SUS440C high hardness stainless steel tube:
SUS440C stainless steel tube has high hardness and good wear resistance. When sanding, it has the disadvantage of being relatively viscous and heating up quickly, but it is easier to sand than any carbon steel and it is much easier to cut with a hand saw. The annealing temperature of 440C is very low, the hardness usually reaches HRC56-58, and the corrosion resistance and toughness are very strong.
SUS440C VS SUS304
SUS304 is austenitic stainless steel with good plasticity and good cold workability. At the same time, due to its austenitic structure, it is non-magnetic and cannot be adsorbed by magnets. It is difficult to increase its strength by heat treatment, and its corrosion resistance is excellent.
SUS440C is martensitic stainless steel. Its microstructure is martensitic metallurgical structure. Its mechanical strength is higher than that of SUS304, and its mechanical properties can be further enhanced by heat treatment.
For performance-determined use, SUS304 is mostly used to make stainless steel daily necessities, containers, etc., while SUS440 is used for manufacturing tools, tools, and other applications requiring high strength and hardness.
U-tubes are made of precision straight tubes. These precision straight tubes are completed after cold rolling and bright annealing. In order to meet the technical conditions of our customers, every step of the process is strictly controlled.
U-tubes are mainly divided into two categories according to materials: stainless steel U-tubes and alloy steel U-tube
U-tube explanation
a……………….The difference in length between two straight pipe sections
c…………..The tangent spacing of the outer wall of the elbow
Da…………nominal steel pipe outer diameter
E…………..The distance between the outer diameters of the two straight ends
f……………the distance between the ends of the two straight ends
l…………… straight tube length
Lg…………. straight pipe section plus total length of pipe
Rm………..nominal bending radius
S………….nominal wall thickness
Smin…….The minimum wall thickness at the back of the elbow
t……………the bend deviates from the horizontal distance
So………..Standard minimum wall thickness
U-tube
Heat treatment
If requested by the customer, we add a straight pipe section with a minimum of 150mm according to the elbow.
Heat treatment is performed.
The computer controls the heat treatment furnace and records all the data.
The tube is filled with a protective gas – argon.
We can provide all the forms of annealing:
Solution annealing
Stress relief annealing
Stabilized annealing
Technical Parameters
Outer diameter: 12.7-38 mm
The bending radius is from 1.5 times the outer diameter to 1250 mm. The outer diameter is over 28mm,
The minimum bend radius can be further discussed.
Straight pipe length is the shortest 1000mm
Straight pipe length up to 12000mm
The bending radius is below 1000mm and heat treatment is required.
Bent pipe technology standard
Technical Standard 7-2-1179
DIN 2879, TEMA RCB 2.31
Can be specified according to customer requirements. Can also follow some general techniques
Specifications.
Hydrostatictest
All U-tubes are subjected to a hydrostatic test after heat treatment.
The test time is not less than 5 seconds at the set pressure.
All tubes were blown dry and carefully cleaned after the test.
Measuring, cutting, deburring, cleaning
Accurately measure U-tubes according to relevant standards or customer requirements.
All pipes should be cut to length, deburred, and air dried to the inner wall.
Seal the ends with a plastic cap before packing.
Package
Use a strong, and depending on the distance to the destination, choose an open or sealed wooden case with a maximum weight of 8,000kg.
Both ends of the pipe are sealed with a plastic cap
Each elbow radius specification is vertically separated
Each row is separated by a chlorine-free plastic sheet every two meters
Each bundle of tubes is wrapped in plastic sheet
Customers can provide packaging drawings or Sandvik ready to package
The packing list should be packed in a plastic bag and placed in a wooden box for detailed review at the time of arrival – including all bend radii and pipe lengths.