Stainless Steel Pipe
Stainless steel is durable, resists corrosion from caustic chemicals, corrosive fluids, oils, and gases, and withstands pressure and high temperatures.
Stainless Steel Pipe is a hollow long round steel, mainly used in petroleum, chemical, medical, food, light industry, mechanical instrument and other industrial pipelines and mechanical structures. Stainless steel pipes are used for high-temperature applications. Stainless steel pipe has add the alloying elements like Nickel and Chromium to the common steel alloy. This addition of the alloying elements enhances the resistance of the steel to corrosion in harsh applications.
As a general rule, any steel alloy that has at least 10.5% of chromium may be considered stainless steel. Austenitic Stainless Steel (Especially series 300 chromium-nickel alloys like 304, 310S, 316, 321, 347, etc), these are the most common grades of stainless steel. Grade 304/304L is the most common austenitic stainless steel that suits most corrosive applications. Any other grade in the 300 series enhances the basic features of SS304.
Seamless or Welded stainless steel pipes or Tubes according to the Standard ASTM A312, ASTM A213, ASTM A269, ASTM AB676, ASTM B677, the main grades are TP304, TP304L, TP310S, TP316, TP316L, 316Ti, TP317, TP317L, TP321, TP347, TP347H, S31254, N08367, N08926, N08904. Each alloy has a specific structure and chemical composition and mechanical properties.
ASTM A312 – For high temperature and general corrosive for seamless, welded, and heavy cold worked austenitic stainless steel pipes.
ASTM A213 stainless tubing for boiler, heat exhanger, covers the seamless ferric carbon steel and austenitic alloy stainless steel tube, applied for boiler, superheater, and heat-exchanger steel tubes.
ASTM A269 – General use stainless tubing for common application in seamless and welded.
ASME SB677 – Extremely corrosive resistance, covers the UNS N08904 (904L), UNS N08925, UNS N08926 (alloy 926), in seamless, of cold-drawn, and hot finished steel pipe and steel tube for the extremely corrosive services.
Grade of stainless steel pipe
Material | ASTM Grade | UNS Grade | DIN Grade | JIS Grade | Steel Name |
Austenitic | TP 304 | S30400 | 1.4301 | SUS304TB | X5CrNi18-20 |
TP 304L | S30403 | 1.4306 | X2CrNi19-11 | ||
TP 304L | S30403 | 1.4307 | SUS304LTB | X2CrNi18-9 | |
TP 304H | S30409 | 1.4948 | SUS304HTB | X6CrNi18-10 | |
TP 310S | S31008 | 1.4845 | SUS310STB | X8CrNi25-21 | |
TP 310H | S31009 | ||||
1.4335 | X1CrNi25-21 | ||||
TP 316 | S31600 | 1.4401 | SUS316TB | X5CrNiMo17-12-2 | |
TP 316L | S31603 | 1.4404 | SUS316LTB | X2CrNiMo17-12-2 | |
TP 316H | S31609 | 1.4918 | SUS316HTB | X6CrNiMo17-13-2 | |
TP 316Ti | S31635 | 1.4571 | SUS316TiTB | X6CrNiMo17-12-2 | |
TP 321 | S32100 | 1.4541 | SUS321TB | X6CrNiNb18-10 | |
TP 312H | S32109 | 1.4941 | SUS321HTB | X6CrNiTiB18-10 | |
TP 347 | S34700 | 1.455 | SUS347TB | X6CrNiNb18-10 | |
TP 347H | S34709 | 1.4912 | SUS347HTB | X7CrNiNb18-10 | |
Ferritic & Martensitic | TP 405 | S41500 | 1.4002 | SUS 405TB | X6CrAl13 |
TP 410 | S41000 | 1.4006 | SUS 410TB | X12Cr13 | |
TP 430 | S43000 | 1.4016 | SUS 430TB | X6Cr17 | |
Ferritic / Austenitic | UNS S31803 | ||||
2205 | UNS S32205 | 1.4462 | X2CrNiMoN22-5-3 | ||
2507 | UNS S32750 | 1.441 | X2CrNiMoN25-7-4 | ||
UNS S32760 | 1.4501 | X2CrNiMoCuWN25-7-4 |
Standard of stainless steel pipe
A 213 / SA 213 | Seamless Ferritic and Austenitic Alloy-steel Boiler,Superheater and Heat-Exchanger Tubes |
A 249 / SA 249 | Welded Austenitic Steel Boiler,Superheater, Hear Exchanger and Condenser Tubes |
A 268 / SA 268 | Seamless and Welded Ferritic and Martensitic Stainless Steel Tubing for General Service |
A 269 | Seamless and Welded Austenitic Stainless Steel Tubing for General Service |
A 312 / SA 312 | Seamless,Welded and Heavily Cold Worked Austenitic Stainless Steel Pipes |
A 376 / SA 376 | Seamless Austenitic Steel Pipe for High-temperature Service |
A 688 / SA 688 | Seamless and Welded Austenitic Stainless Steel Feedwater Heater Tubes |
A 789 / SA 789 | Seamless and Welded Ferritic/Austenitic Stainless Steel Tubing for General Service |
A 790 / SA 790 | Seamless and Welded Ferritic/Austenitic Stainless Steel Pipe |
A 999 / SA 999 | General Requirement for Alloy and Stainless Steel Pipe |
A 1016 / SA 1016 | General Requirement for Ferritic Alloy Steel, Austenitic Alloy Steel and Stainless Steel Tubes |
European Standard | |
DIN EN 10216-5 | Seamless Steel Tubes for Pressure Purposes |
DIN EN 10217-7 | Welded Steel Tubes for Pressure Purposes |
DIN EN 10297-2 | Seamless Steel Tubes for Mechanical and General Engineering Purposes |
DIN EN 10305-1 | Steel Tubes for Precision Application |
German Standard | |
DIN 11850 | Stainless Steel Tubes for the Food and Chemical Industries-Dimensions, Materials |
DIN 17455 | General Purpose Welded Circular Stainless Steel Tubes |
DIN 17456 | General Purpose Seamless Circular Stainless Steel Tubes |
DIN 17457 | Welded Circular Austenitic Stainless Steel Tubes Subject to Special Requirement |
DIN 17458 | Seamless Circular Austenitic Stainless Steel Tubes Subject to Special Requirement |
DIN 28180 | Seamless Steel Tubes for Heat-exchanger |
DIN 11850 | Welded Tubes and Pipe for Food, Beverages,Chemical&Pharmaceuticals Industry |
Russian Standard | |
GOST 9941 | Seamless and Warm-deformed Tubes Made from Corrosion-resistant Steel |
Norsok Standard | |
Norsok M – 650 | Qualification of Manufacturers of Special Material |
Norsok M – 630 | Material Data Sheets and Element Data Sheerts for Piping |
Chemical Composition:
Grade | UNS | C≤ | Mn | P≤ | S≤ | Si≤ | Cr | Mo | Ni |
TP304 | S30400 | 0.08 | 2 | 0.045 | 0.03 | 1 | 18.0-20.0 | – | 8.0-11.0 |
TP304L | S30403 | 0.035 | 2 | 0.045 | 0.03 | 1 | 18.0-20.0 | – | 8.0-12.0 |
TP316 | S31600 | 0.08 | 2 | 0.045 | 0.03 | 1 | 16.0-18.0 | 2.00-3.00 | 10.0-14.0 |
TP316L | S31603 | 0.035 | 2 | 0.045 | 0.03 | 1 | 16.0-18.0 | 2.00-3.00 | 10.0-14.0 |
316Ti | S31668 | 0.08 | 2 | 0.035 | 0.03 | 1 | 16.0-19.0 | 1.80-2.50 | 10.0-14.0 |
TP317 | S31700 | 0.08 | 2 | 0.045 | 0.03 | 1 | 18.0-20.0 | 3.0-4.0 | 11.0-15.0 |
TP317L | S31703 | 0.035 | 2 | 0.045 | 0.03 | 1 | 18.0-20.0 | 3.0-4.0 | 11.0-15.0 |
TP321 | S32100 | 0.08 | 2 | 0.045 | 0.03 | 1 | 17.0-19.0 | – | 9.0-12.0 |
TP310S | S31008 | 0.08 | 2 | 0.045 | 0.03 | 1 | 24.0-26.0 | 0.75 | 19.0-22.0 |
TP347 | S34700 | 0.08 | 2 | 0.045 | 0.03 | 1 | 17.0-19.0 | – | 9.0-13.0 |
S31254 | 0.02 | 1 | 0.03 | 0.01 | 0.8 | 19.5-20.5 | 6.0-6.5 | 17.5-18.5 | |
N08367 | 0.03 | 2 | 0.04 | 0.03 | 1 | 20.0-22.0 | 6.0-7.0 | 23.5-25.5 | |
N08926 | 0.02 | 2 | 0.03 | 0.01 | 0.5 | 24.0-26.0 | 6.0-7.0 | 19.0-21.0 | |
N08904 | 0.02 | 2 | 0.04 | 0.03 | 1 | 19.0-23.0 | 4.0-5.0 | 23.0-28.0 | |
N08925 | 0.02 | 1 | 0.045 | 0.03 | 0.5 | 19.0-21.0 | 6.0-7.0 | 24.0-26.0 |
The high amounts of molybdenum and chromium content in 2205 offer strength, improved pitting and consistent stress corrosion cracking resistance. 2205 integrates the best features of austenitic and ferritic steels (as well as nearly equal amounts of austenite and ferrite) and can be welded with common stainless steel welding techniques – its uniform composition minimizes localized corrosion.
Specifications – Duplex 2205
- ASTM: A790, A815, A182
- ASME: SA790, SA815, SA182
Chemical Composition – Duplex 2205
C | Cr | Fe | Mn | Mo | N | Ni | P | S | Si |
Max | Max | Max | Max | Max | |||||
.03% | 22%-23% | BAL | 2.0% | 3.0% -3.5% | .14% – .2% | 4.5%-6.5% | .03% | .02% | 1% |
Design Features – Duplex 2205
- High Strength
- Exceptional uniform corrosion resistance
- Better heat conductivity and lower thermal expansion than austenitic steels
- Resistance to stress corrosion cracking
- Resistance to erosion
- Resistance to corrosion fatigue
- Resistance to pitting
- Resistance to crevace corrosion
- Resistance to sulfide stress corrosion cracking
Typical Applications – Duplex 2205
Some of the typical applications of duplex steel grade 2205 are listed below:
- Heat exchangers, tubes and pipe for production and handling of gas and oil
- Heat exchangers and pipes in desalination plants
- Pressure vessels, pipes, tanks and heat exchangers for processing and transport of various chemicals
- Pressure vessels, tanks and pipes in process industries handling chlorides
- Rotors, fans, shafts and press rolls where the high corrosion fatigue strength can be utilized
- Cargo tanks, piping and welding consumables for chemical tankers
Physical Properties
The physical properties of grade 2205 stainless steels are tabulated below.
Grade | Density (kg/m3) | Elastic Modulus (GPa) | Mean Co-eff of Thermal Expansion (μm/m/°C) | Thermal Conductivity (W/m.K) | Specific Heat 0-100°C ( J/kg.K) | Electrical Resistivity (nΩ.m) | |||
0-100°C | 0-315°C | 0-538°C | at 100°C | at 500°C | |||||
2205 | 782 | 190 | 13.7 | 14.2 | – | 19 | – | 418 | 850 |
- Grade S31803 has similar physical properties to that of S32205.
Corrosion Resistance
Grade 2205 stainless steel exhibits excellent corrosion resistance, much higher than that of grade 316. It resists localized corrosion types like intergranular, crevice and pitting. The CPT of this type of stainless steel is around 35°C. This grade is resistant to chloride stress corrosion cracking (SCC) at temperatures of 150°C. Grade 2205 stainless steels are apt replacements to austenitic grades, especially in premature failure environments and marine environments.
The super duplex gradesare even more resistant to corrosion.
Heat Resistance
- The high chromium content of duplex stainless steels that protects against corrosion, causes embrittlement at temperatures over about 300°C.
- At low temperatures duplex stainless steels have better ductility than the ferritic and martensitic grades. Duplex grades can readily be used down to at least -50°C.
Fabrication
Fabrication of all stainless steelsshould be done only with tools dedicated to stainless steel materials. Tooling and work surfaces must be thoroughly cleaned before use. These precautions are necessary to avoid cross contamination of stainless steel by easily corroded metals that may discolour the surface of the fabricated product.
Welding
Most standard welding methods suit this grade, except welding without filler metals, which results in excess ferrite. AS 1554.6 pre-qualifies welding for 2205 with 2209 rods or electrodes so that the deposited metal has the right balanced duplex structure.
Adding nitrogen to the shielding gas ensures that adequate austenite is added to the structure. The heat input must be maintained at a low level, and the use of pre or post heat must be avoided. The co-efficient of thermal expansion for this grade is low; hence the distortion and stresses are lesser than that in austenite grades.
Machinability
Although machinable, the high strengths of duplex stainless steels makes machining difficult. As an example, machining of 2205 is around 20% slower than for 304.
Machining can be enhanced by using the following rules:
- Cutting edges must be kept sharp. Dull edges cause excess work hardening.
- Cuts should be light but deep enough to prevent work hardening by riding on the surface of the material.
- Chip breakers should be employed to assist in ensuring swarf remains clear of the work
- Low thermal conductivity of austenitic alloys results in heat concentrating at the cutting edges. This means coolants and lubricants are necessary and must be used in large quantities.
Heat Treatment
Duplex stainless steelscannot be hardened by heat treatment. They can however be work hardened.
Solution treatment or annealing can be done by rapid cooling after heating to around 1100°C.
Weldability
Duplex stainless steelshave good weldability. All standard welding processes can be used. They are not quite as easily welded as the austenitic grades but low thermal expansion in duplex grades reduces distortion and residual stresses after welding. The recommended filler material for 2205 stainless steelis 2209.
Grade Reasons for choosing the grade
- 904L -Better formability is needed, with similar corrosion resistance and lower strength.
- UR52N+ High resistance to corrosion is required, e.g. resistance to higher temperature seawater.
- 6%Mo – Higher corrosion resistance is required, but with lower strength and better formability.
- 316L – The high corrosion resistance and strength of 2205 are not needed. 316L is lower cost.
Duplex 2507 (UNS S32750) is a super duplex stainless steel with 25% chromium, 4% molybdenum, and 7% nickel designed for demanding applications which require exceptional strength and corrosion resistance, such as chemical process, petrochemical, and seawater equipment.
Duplex Stainless Steels, also referred to as austeniticferritic stainless steels, are a family of grades having around equal proportions of austenite and ferrite.
These steels have a duplex microstructure which contributes to their high strength and high resistance to stress corrosion cracking.
Duplex steels offer high resistance to uniform and local corrosion because of their high content of nitrogen, chromium and molybdenum. Duplex stainless steels have good weldability.
There are three groups of duplex stainless steels that include the following:
- Lean Duplex
- Standard Duplex
- Super Duplex.
Standards
- ASTM/ASME A240 – Specification for Chromium and Chromium-Nickel Stainless Steel Plate, Sheet, and Strip for Pressure Vessels and for General Applications
- EURONORM 1.4410 – X2 Cr Ni MoN 25.7.4
- AFNOR Z3 CN 25.06 Az
S32750 or Duplex 2507
Duplex 2507 is a super duplex stainless steel developed for applications that demand high strength and corrosion resistance. Alloy 2507 has 25% chromium, 4% molybdenum, and 7% nickel.
This high molybdenum, chromium and nitrogen content causes high resistance to chloride pitting and crevice corrosion attack and the duplex structure provides 2507 with exceptional resistance to chloride stress corrosion cracking.
Using Duplex 2507 must be restricted to applications below 600° F (316° C). Extended elevated temperature exposure can reduce both the toughness and corrosion resistance of alloy 2507.
Duplex 2507 has good mechanical properties. Often a light gauge of 2507 material can be used to achieve the same design strength of a thicker nickel alloy. The resulting weight savings can considerably reduce the overall cost of fabrication.
Properties of Super Duplex Steel 2507 or S32750
- High resistance to chloride stress corrosion cracking.
- High Strength.
- Combination of properties given by austenitic and ferritic structure.
- Good weldability and workability.
- Superior resistance to chloride pitting and crevice corrosion.
- Good general corrosion resistance.
- Suggested for applications up to 600° F.Stainless Steel S32760
Applications of S32750 Super Duplex Stainless Steel
Alloy 2507 (UNS S32750) is a super duplex stainless steel with 25% chromium, 4% molybdenum, and 7% nickel designed for demanding applications which require exceptional strength and corrosion resistance, such as chemical process, petrochemical, and seawater equipment. The steel has excellent resistance to chloride stress corrosion cracking, high thermal conductivity, and a low coefficient of thermal expansion. The high chromium, molybdenum, and nitrogen levels provide excellent resistance to pitting, crevice, and general corrosion.
The applications of S32750 super duplex stainless steel are:
- Desalination Equipment.
- Chemical process pressure vessels, piping and heat exchangers.
- Marine Applications.
- Flue Gas Scrubbing Equipment.
- Pulp & Paper Mill Equipment.
- Offshore Oil production/technology.
- Oil and gas industry equipment.
Chemical Analysis
Typical Values (Weight %)
Carbon | Chromium | Nickel | Molybdenum | Nitrogen | Others |
---|---|---|---|---|---|
0.020 | 25 | 7 | 4.0 | 0.27 | S=0.001 |
PREN = [Cr%] = 3.3 [Mo%] = 16 [N %] ≥ 40 |
Mechanical Properties
Mechanical and Physical Properties
2507 combines high tensile and impact strength with a low coefficient of thermal expansion and high thermal conductivity. These properties are suitable for many structural and mechanical components. The low, ambient, and elevated temperature mechanical properties of 2507 sheet and plate are shown below. All of the test data shown are for samples in the annealed and quenched condition.
2507 is not recommended for applications which require long exposures to temperatures in excess of 570°F because of the increased risk of a reduction in toughness. The data listed here are typical for wrought products and should not be regarded as a maximum or minimum value unless specifically stated.
Properties
0.2% Offset Yield Strength, ksi
Ultimate Tensile Strength, ksi
1% Offset Yield Strength, ksi
Elongation in 2 inches, %
Hardness, Rockwell C
Impact Energy, ft-lbs
80 min.
116 min.
91 min.
15 min.
32 max
74 min.
Low Temperature Impact Properties
Temperature °F | RT | 32 | -4 | -40 |
---|---|---|---|---|
Ft-lbs | 162 | 162 | 155 | 140 |
Temperature °F | -76 | -112 | -148 | -320 |
Ft-lbs | 110 | 44 | 30 | 7 |
Elevated Temperature Tensile Properties
Temperature °F | 68 | 212 | 302 | 392 | 482 |
---|---|---|---|---|---|
0.2% Offset Yield Strength, ksi | 80 | 65 | 61 | 58 | 55 |
Ultimate Tensile Strength, ksi | 116 | 101 | 98 | 95 | 94 |
Values obtained for hot rolled plates (th ≤ 2″). Alloy 2304 must not be used for a long time at temperatures higher than 300°C (572°F), where precipitation hardening phenomenon occurs.
Physical Properties
Density : 7,800 kg/m3 – 0.28 lb/in3
Interval Temper °C | Thermal expansion ax10M-bK-1 | °C | Resistivity (μ_ cm) | Thermal conductivity (W.m-1.K-1) | Specific heat (J.kg-1.K-1 | Young modulus E (GPa) | Shear modulus G (GPa) |
---|---|---|---|---|---|---|---|
20-100 | 13 | 20 | 80 | 17 | 450 | 200 | 75 |
20-100 | 13 | 100 | 92 | 18 | 500 | 190 | 73 |
20-200 | 13.5 | 200 | 100 | 19 | 530 | 180 | 70 |
20-300 | 14 | 300 | 105 | 20 | 560 | 170 | 67 |
Processing
Hot Forming
2507 should be hot worked between 1875 F and 2250 F. This should be followed by a solution anneal at 1925F minimum and a rapid air or water quench.
Cold Forming
Most of the common stainless steel forming methods can be used for cold working 2507. The alloy has a higher yield strength and lower ductility than the austenitic steels so fabricators may find that higher forming forces, increased radius of bending, and increased allowance for springback are necessary. Deep drawing, stretch forming, and similar processes are more difficult to perform on 2507 than on an austenitic stainless steel. When forming requires more than 10% cold deformation, a solution anneal and quench are recommended.
Heat Treatment
2507 should be solution annealed and quenched after either hot or cold forming. Solution annealing should be done at a minimum of 1925 F. Annealing should be followed immediately by a rapid air or water quench. To obtain maximum corrosion resistance, heat treated products should be pickled and rinsed.
Material to UNS S32760 is described as a super duplex stainless steel with a microstructure of 50:50 austenite and ferrite.
UNS S32760 is a duplex stainless steel especially designed for service in aggressive chloride-containing environments and has additions of W and Cu compared to UNS S32750. It has very good resistance to localized corrosion and stress corrosion cracking in combination with high mechanical strength.
The characteristic features of high strength and corrosion resistance exhibited by the dual microstructure (50% Austenite, 50% Ferrite) associated with Duplex Stainless Steels, are enhanced by a further addition of Chromium (to 25%), and also Tungsten and Copper.
The alloy’s pitting and Crevice Corrosion resistance is better than Standard F51 duplex, The pitting index (PREN) is increased to 40 min from standard F51 Duplex value of 33 min.
Thin sections (Tubulars) are capable of being cold worked to give yield strength of 105 KSI min.
To optimise mechanical properties, avoid clinking, and to avoid deleterious intermetallics within the microstructure; special high temp forming and heat treatment control practices must be followed during processing.
Chemical composition
C | Si | Mn | P | S | Cr | Ni | Mo | Cu | N | W | PREN | Fe | |
---|---|---|---|---|---|---|---|---|---|---|---|---|---|
Min | • | • | • | • | • | 24.00 | 6.00 | 3.00 | 0.50 | 0.20 | 0.50 | 40.00 | 0.00 |
Max | 0.03 | 1.00 | 1.00 | 0.030 | 0.010 | 26.00 | 8.00 | 4.00 | 1.00 | 0.30 | 1.00 | • | 0.00 |
Mechanical properties
Condition: Solution Annealed and Water Quenched.
U.T.S | 109 KSI Min | (750 N/mm2) |
---|---|---|
0.2% Proof Stress | 80 KSI Min | (550 N/mm2) |
Elongation | 25 % | |
Red of Area | 45 % | |
CVN Impacts @ -46°C (-50°F) | 45 Joules | (33 ft-lbf) |
NACE MR0175 limits the supply hardness to 28 HRC max.
Material to UNS S32760 is described as a super duplex stainless steel with a microstructure of 50:50 austenite and ferrite.
The steel combines high mechanical strength (typically up to 600 MPa yield strength) and good ductility with outstanding corrosion resistance to marine environments and a wide, diverse range of oil & gas production environments. The alloy is supplied with a PREN(Pitting Resistance Equivalent) at >= 40.0 which guarantees high resistance to pitting corrosion. In addition, the steel offers high resistance to crevice corrosion and stress corrosion cracking.
Ambient and sub-zero (down to minus 50°C) notch ductility is good. These attributes mean that this super duplex steel can be used successfully as an alternative to 300 series stainless steel (such as type 316), standard 22% Cr duplex steel and precipitation hardening stainless steels. Where appropriate the alloy can be considered in lieu of more costly Grade 5 titanium or nickel based alloys.
Machinability & Welding
The machining and welding of this grade of super duplex stainless steel presents no particular problems. Guidance notes are available upon request.
Typical Applications:
High impact strength at sub-zero temperatures, UNS S32760 displays excellent corrosion resistance.

UNS S32760 is characterized by:
- High resistance to stress corrosion cracking in halide containing environments.
- High resistance to pitting and crevice corrosion.
- High resistance to general corrosion.
- High mechanical strength.
- High resistance to erosion corrosion and corrosion fatigue.
It is widely used in oil & gas, hydropower, pressure vessels, pulp & paper, structural components and chemical tankers.
Corrosion resistance
Material | % Mo | CCCT, °C (°F) | CPT, °C (°F) | PREN |
---|---|---|---|---|
316L | 2.1 | < -2.22 (28) | 20 (68) | 24 |
2205 | 3.1 | 20 (68) | 49 (120) | 35 |
904L | 4.4 | 24 (75) | 54.4 (130) | 36 |
UNS S32760 | 3.5 | 42.2 (108) | 82 (180 ) | 41 |
AL-6XN | 6.2 | 43.3 (110) | 82 (180 ) | 44 |
625 | 9 | 45 (113) | – | 51 |
C22 | 13 | – | – | 64 |
C-276 | 15.5 | 54.4 (130) | > 103 (217) | 67 |
Dual-phase steel (DPS) is a high-strength steel that has a ferrite and martensitic microstructure. DPS starts as a low or medium carbon steel and is quenched from a temperature above A1 but below A3 on a continuous cooling transformation diagram.
Dual-phase steel (the Super Duplex Stainless Steel, referred to as SDSS), also known as Dual Phase Steel.
Martensitic or austenitic and ferritic matrix two-phase structure is consisting of steel. Generally ferritic and austenitic phase structure that composed of steel called duplex stainless steel, ferritic and martensitic phase structure that composed of steel called a dual-phase steel. The dual-phase steel is low carbon steel or high strength low alloy steel after the heat treatment or control the rolling of the critical region. A typical dual-phase steel yield strength σs 310MPa tensile strength σb is 655MPa. Duplex steel for the manufacture of cold punching, deep drawing and forming of complex components can also be used as a pipeline steel, chain, cold drawn steel wire, prestressed reinforced.
Nature:
It is mainly composed of ferrite and martensite steel, which can be low-carbon steel or low alloy steel by the treatment or control rolling of the critical region. The type of steel has high strength and high ductility, good co-ordination. Now, it has become a high strength, good formability new stamping steel successful for the auto industry.
Through proper control of chemical composition and heat treatment process, both the advantages of ferritic stainless steel and austenitic stainless steel duplex stainless steel due to the characteristics of the two-phase structure, it austenitic stainless steel with excellent toughness and weldability and iron ferritic stainless steel with high strength and resistance to chloride stress corrosion combined with superior performance of duplex stainless steel welding of structural materials has developed rapidly since the 1980s has become a martensitic, Austria steel type’s size and ferritic stainless steel side by side.
Special Piping Materials has always been at the forefront of the industry due to the company’s determination to supply its clients with the materials grades that best suit their requirements.
MATERIALS
An example of the range of materials we supply are as follows:
- Super Duplex (S32760 and S32750 / 2507)
- Duplex (S31803 / 2205)
- 6% Moly (S31254)
- Nickel Alloys (Alloy 400, 625, 800, 825, etc)
- Stainless Steels (316L, 304L, 904L, 310, 321, etc.)
Duplex becomes brittle at extreme temperatures so its use is normally restricted to a maximum temperature of 300 degrees and shows signs of embrittlement at –50 degrees.
The Benefits of using Duplex Stainless Steel Pipe:
- Stronger than 300 series stainless steel which also brings weight advantages
- High resistance to pitting, crevice corrosion and stress corrosion cracking
- Higher heat conductivity and lower thermal expansion than austenitic steels
Duplex Stainless Steel Pipe is used in:
- Pipes for production and transportation of oil and gas
- Structural and mechanical components
- Heat exchangers
- Cooling pipes
Inconel 625/UNS N06625/Nickel 625/Alloy 625/ W.Nr.2.4856/Super Alloy/Corrosion resistant alloy/NS336/0Cr20Ni65Mo10Nb4
Size:T10-40mm * W1500mm * L1500mm
Forms: Pipes, Tubes, Plates, Sheets, Round Bar,Wire, Forging
Inconel 625 Chemical composition:
Alloy | % | Ni | Cr | Mo | Nb+N | Fe | Al | Ti | C | Mn | Si | Cu | P | S |
625 | Min. | 58 | 20 | 8 | 3.15 |
|
|
|
|
|
|
|
|
|
Max. |
| 23 | 10 | 4.15 | 5 | 0.4 | 0.4 | 0.1 | 0.5 | 0.5 | 0.5 | 0.015 | 0.015 |
Inconel 625 Pysical properties:
Density | 8.4 g/cm³ |
Melting point | 1290-1350°C |
Specifications
1) Specifications: OD: 10 -325mm and THK: 1 – 20mm
2) Grades: 316LMod, 724L,1.4435
3) Made according to the standards of ATSM, AISI, DIN, JIS, EN10216-5
4) Chemical Composition:
C:max0.03, Si:max1.0, Mn:max2.0, P:max0.040, S:max0.015, Cr:17.0-19, Ni:13.0-15.0 , Mo:2.50-3.0
Monel 400 Pipes and Tubes is a mixture of Nickel, Copper along with Iron, Carbon, Manganese, and Silicon content. It provides outstanding corrosion resistance in acidic as well as alkaline environments. This alloy contains higher Nickel and Copper content that exhibit higher mechanical strength, low thermal expansion, and high thermal conductivity.
ASTM B163 seamless tube standard: Monel 400 seamless tube
ASTM B165 standard: Monel 400 seamless pipe, Monel 400 seamless tube
ASTM B474 welded pipe standard: Monel 400 EFW pipe
Monel 400/K500 Pipe tube size:
Seamless Pipe size: 4 to 219mm; W. T.: 0.5 to 20mm
Seamless Tube Size: 3.35 mm To 101.6 mm (OD)
Welded Pipe size: 5.0 mm – 1219.2 mm
Monel 400/K500 Pipes & Tubes Chemical Composition:
Grade | C≤ | Mn≤ | Si | S≤ | Cu | Fe≤ | Ni |
Monel400 | 0.3 | 2 | 0.5 | 0.024 | 28.0-34.0 | 2.5 | 63 |
K500 | 0.25 | 1.5 | 0.5 | 0.01 | 27.0-33.0 | 0.5-2 | 63 |
Monel 400/K500 Pipes & Tubes Mechanical Properties:
Grade | Density | Melting Point | Tensile Strength | Yield Strength (0.2%Offset) | Elongation |
400 | 8.8 g/cm3 | 1350 °C (2460 °F) | Psi – 80,000, MPa – 550 | Psi – 35,000, MPa – 240 | 40 % |
K500 | 8.44 g/cm3 | 1350 °C (2460 °F) | Psi – 1,60,000, MPa – 1100 | Psi – 1,15,000, MPa – 790 | 20 % |
Equivalent Grades for Monel 400 Seamless and Welded Pipes:
STANDARD | WERKSTOFF NR. | UNS | JIS | BS | GOST | AFNOR | EN |
Monel 400 | 2.4360 | N04400 | NW 4400 | NA 13 | МНЖМц 28-2,5-1,5 | NU-30M | NiCu30Fe |
K500 | 2.4375 | N05500 | – | – | – | – | – |
Test:
Hardness Test
Flattening Test
Pitting Resistance Test
Chemical Analysis – Spectro Analysis
Micro and MacroTest
Flaring TestIntergranular Corrosion (IGC) Test
Mechanical Testing Such as Tensile of Area
Positive Material Identification (PMI Testing)
904L Stainless steel consists of Chromium, Nickel, Molybdenum and Copper contents, these elements make 904L stainless steel excellent properties to resist corrosion in dilute sulfuric acid, because of the addition of Copper, 904L commonly is used in high pressure and corrosion environment where 316L and 317L perform poorly.
Standards
ASTM A 312 – seamless, welded, and heavily cold worked austenitic stainless steel pipes
ASTM A 213 – seamless ferritic and austenitic alloy-steel boiler, super heater, and heat-exchanger tubes
ASTM A 269 – seamless and welded austenitic stainless steel tubing for general service
ASTM B 677 – uns n08904, uns n08925, and uns n08926 seamless pipe and tube
Seamless tube is extruded and drawn from a billet while welded tube is produced from a strip that is roll formed and welded to produce a tube.
Welded tube is considerably less expensive than seamless tube and is readily available in long continuous lengths.
Electric Resistance Welded (ERW) pipe is manufactured by cold forming a flat steel strip into a rounded tube and passing it through a series of forming rollers to obtain a longitudinal seam.
The two edges are then simultaneously heated with a high frequency current and squeezed together to form a bond.
1. 904L Stainless Steel Seamless and Welded Heat-Exchanger and Condenser Pipe and Tubes Specifcation
Standard | ASTM, DIN, GB, AISI, JIS, ISO, etc other International Standards |
Dimensions | ASTM, ASME and API |
Specifications | ASTM A312, A213, A269, B677 |
ERW Pipes & Tubes Size | 1/2″ NB – 24″ NB |
EFW Pipes & Tubes Size | 6″ NB – 100″ NB |
Pipes & Tubes Size | 1/2″ NB – 16″ NB |
Length | Single Random, Double Random & Required Length or As per Customer Requirement |
Schedule | SCH20, SCH30, SCH40, STD, SCH80, XS, SCH60, SCH80, SCH120, SCH140, SCH160, XXS |
Types | SMLS / ERW / EFW / Welded / Fabricated / LSAW Pipes |
Form | Round Pipes/Tubes, Square Pipes/Tubes, Rectangular Pipe/Tubes, Coiled Tubes, “U” Shape, Pan Cake Coils, Hydraulic Tubes |
End | Plain End, Beveled End, Treaded |
Application | Food & Beverage Industry, Construction Industry, Nuclear, Thermal & Power Plants, Petrochemical, Boilers, Cement Industry, Geothermal Plants, Heat Exchangers, Instrumentation Jobs, Mechanical Jobs, Oil and Gas Equipments and Piping Works |
Package | Plastic caps on botd ends, Steel bundle, Woven bag or acc. to customers’ request |
Stainless Steel 904L Tubing Equivalent
STANDARD | WERKSTOFF NR. | UNS | JIS | AFNOR | BS | KS | EN |
SS 904L | 1.4539 | N08904 | SUS 904L | Z2 NCDU 25-20 | 904S13 | STS 317J5L | X1NiCrMoCu25-20-5 |
904L SS Pipes,Tubes Chemical Properties
Grade |
| C | Mn | Si | P | S | Cr | MO | Ni | CU |
904L | Min | – | – | – | – | – | 19.0 | 4.00 | 23.00 | 1.00 |
max | 0.20 | 2.00 | 1.00 | 0.045 | 0.035 | 23.0 | 5.00 | 28.00 | 2.00 |
SS 904L Mechanical Properties
Density | 8.0 g/cm3 |
Melting Point | 1454 °C (2650 °F) |
Tensile Strength | Psi – 75000 , MPa – 515 |
Yield Strength (0.2%Offset) | Psi – 30000 , MPa – 205 |
Elongation | 35 % |
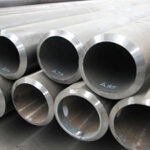
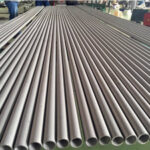
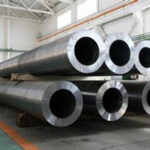
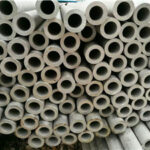
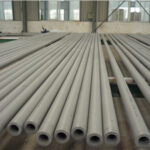
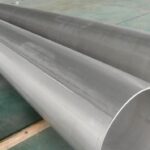
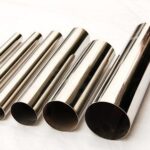
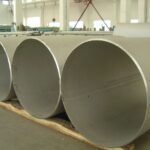